A Distributed Control System (DCS) is a type of automated industrial control system (ICS) used to control geographically distributed processes, such as those in factories, power plants, and other large industrial settings. DCS systems rely on a network of controllers distributed across a facility, allowing for real-time monitoring and control of multiple processes simultaneously. These systems are integral in industries where precise, continuous control is essential. Read on to learn more about the meaning of DCS.
What is a DCS?
A Distributed Control System (DCS) is a computerized control system that streamlines the functionalities of industrial devices used throughout a workspace. A DCS utilizes a wide range of controllers to permit all the parts to converse with one another just as PCs do. These controllers are distributed geographically across a plant to allow for high-speed communication to the control process. When utilizing various kinds of modules, the framework may require diverse correspondence norms, for example, Modbus and Profibus.
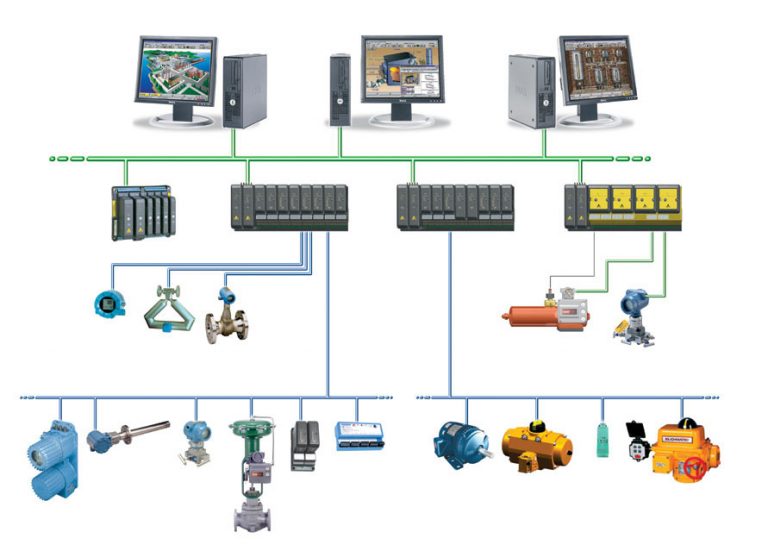
Components of a DCS
A distributed control system or DCS is a control system in which the controller components are not local but are dispersed throughout the system with every component sub-system controlled by one or more controllers. The entire arrangement of controllers is associated by systems for correspondence and observing. DCS is an extremely wide term utilized in an assortment of enterprises, to monitor and control hardware. Below is a list of places that use Distributed Control Systems.
- Radio signals
- Dry cargo and bulk oil carrier ships
- Electrical power grids and electrical generation plants
- Traffic signals
- Water management systems
- Oil refining plants
- Chemical plants
- Sensor networks
- Environmental control systems
History of the DCS
The first Distributed Control System was made by Honeywell in 1969. This new design depended on a vast distributed control to the computer modules. Every one of these modules controlled a few different processors, for the most part, one to four. They were associated with a high-speed data communications link, known as a data highway which made communications between each of the computer modules and the central operator console possible. This plan permitted the administrator to monitor the activity of every local process.
Moving forward, microprocessor-based modules replaced hardwired computer modules in the 1970’s. However, Today’s distributed control systems are much more powerful and faster than the early systems because of advancements in microprocessors and other electronic circuits. The next section of this blog illustrates how a present DCS operates and is shown in the diagram below.
DCS Operation “ The Three Qualities”
A DCS has three main qualities. The first quality is the conveyance of different control capacities into little arrangements of subsystems, which are of semiautonomous, and are interconnected through a rapid correspondence transport. A portion of these capacities incorporate securing information, information introduction, process control, process supervision, revealing data, and the saving and recovery of data.
The second trait of DCS is the computerization of assembling processes by coordinating propelled control techniques. Furthermore, the third quality of the DCS is organizing the entire process as a system. A DCS sorts out the whole control structure as a solitary computerization system where different subsystems are brought together through an appropriate order and data stream.
These qualities of the DCS are shown in the figure below. The essential architecture in a DCS include engineering workstation, operating station or HMI, process control unit or local control unit, smart devices, and a communication system.
Important Features of a DCS
HMI
A DCS can monitor and control through HMI’s, otherwise known as a Human Machine Interface, which gives adequate information to the administrator to charge over different procedures which acts as the center of the system. However, this type of industrial control system covers large areas whereas a DCS covers one region. A DCS uses the whole process plant to control the process as a PC window. Trending, logging and graphical representation of the HMI’s give effective user interface. A Powerful alarming system of a DCS helps operators to respond more quickly to the plant’s shape when needed.
Security
Access to control the various processes leads to plant safety. The DCS design offers a perfect and secure system to handle framework functions for top notch factory automation control. Security is also provided at different levels such as an operator level, engineer level, and an entrepreneur level.
The Handling of Complex Procedures
APLC or Programmable Logic Controller is utilized to control and monitor the procedure parameters at a rapid speed. Click here for more information about PLCs. However, a DCS is preferred for more complex control applications because with a higher number of I/O’s with dedicated controllers, it is able to handle such processes. These are used in assembling processes where the structuring of various products is in multiple procedures such as a batch process control.
Considerations When Choosing a DCS
The bulk of control system decisions include the use of a programmable logic controller (PLC) or a distributed control system (DCS). In some cases one alternative is clearly better for a plant while the choice is not as simple in others. Selecting the control system entails several considerations that will help the customer meet their short-and long-term goals.
Difference between PLC and DCS systems
A PLC is an industrial computer that is built to control manufacturing processes such as robots, high-speed packaging, bottling, and motion control. In the last 20 years, PLCs have gained functionality and provided benefits for small plant applications. PLCs are usually solitary islands of automation that can be unified so they can communicate with one another. PLCs are great for smaller applications that are unlikely to expand in the future.
A DCS distributes controllers throughout the automation system and offers standard guidance, automated monitoring, a systemwide database, and easy-to-share information. DCSs are commonly used in process applications and larger plants, and are easier to maintain throughout the plant’s life cycle for large device applications. To learn more about these technologies, check out our blog: PLC vs. DCS: What’s the Difference.
The Application type determines the platform
PLCs and DCSs are typically suited to one of two forms of production: discrete manufacturing and process manufacturing. Discrete manufacturing facilities, which typically use PLCs, consist of separate manufacturing units which generally assemble components, such as labeling or fill-and-finish applications. Facilities for process manufacturing typically use DCSs, automate continuous and batch processes and enforce formulations consisting of components rather than parts. Process manufacturing facilities calculate their production in bulk. DCS automation is used by large continuous process installations, such as refineries and chemical plants.
Several aspects must be considered when finding the right DCS such as:
- Process size
- Integration needs
- Functionality
- High availability
- Expansion or modification plans
- ROI on the facilities lifespan
Updated on October 31, 2024 by Leanna Cota