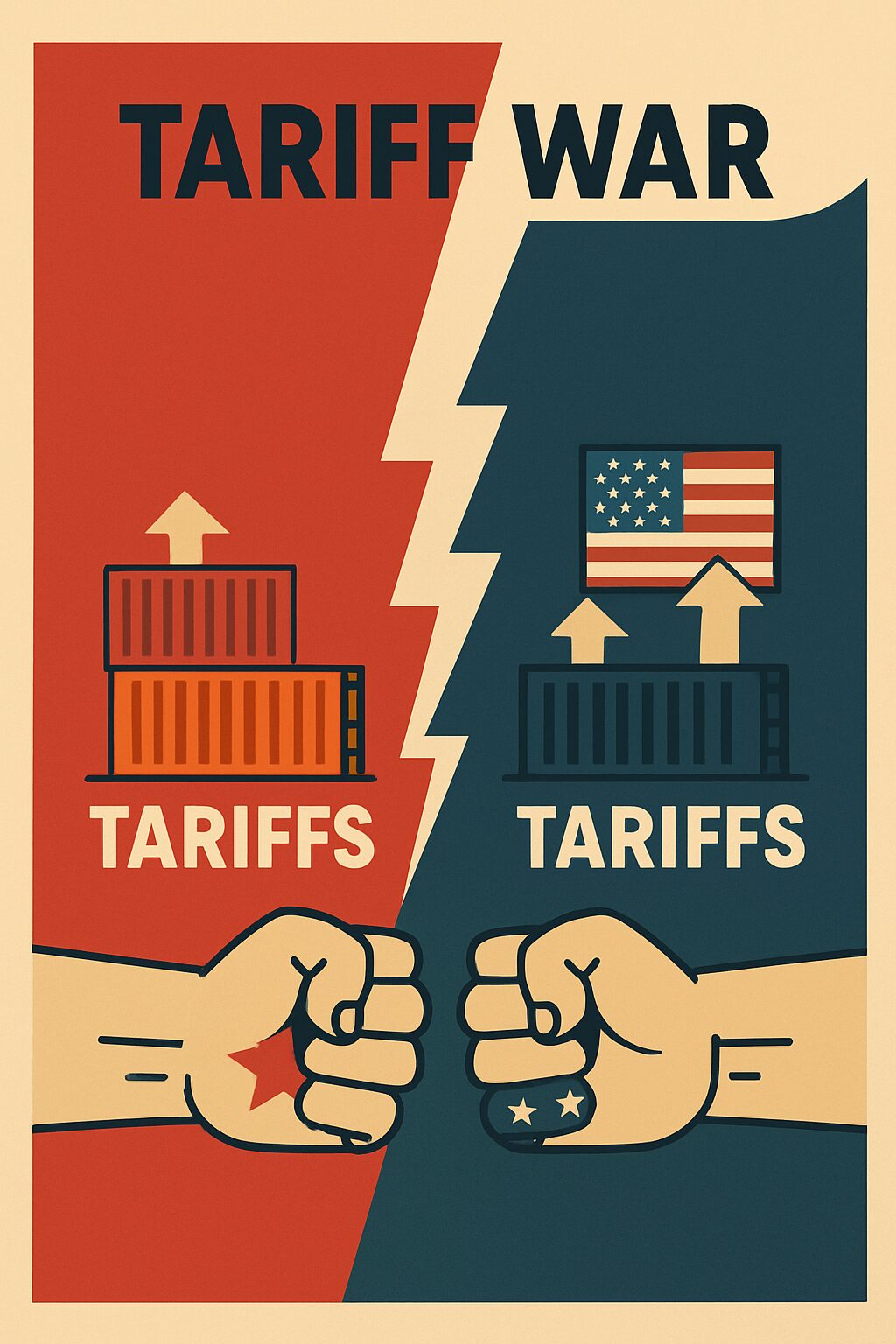
The Impact of Tariffs on Industrial Automation
Industrial automation has become a cornerstone of modern manufacturing, driving efficiency, productivity, and competitiveness. However, the increasing use of tariffs—taxes imposed on imported goods—has introduced new complexities for businesses relying on automation technologies. While tariffs aim to protect domestic industries, they can also disrupt supply chains, increase costs, and slow innovation in industrial automation. This article explores the effects they have on the automation sector.
What Are Tariffs?
There exists the misconception that tariffs are a tax on exporters. However, that simply isn’t true. A tariff is an import tax that gets put upon the importing company not the exporting company. Typically the importing party pays the tariff then in turn passes the cost of the onto their customers by marking up the price of the goods imported in.
How Tariffs Affect Industrial Automation
1. Increased Costs for Automation Components
Many industrial automation systems rely on imported components, such as robotic arms, sensors, controllers, and motors. When tariffs are imposed on these goods, manufacturers face higher procurement costs. For example, U.S. tariffs on Chinese-made automation parts have forced companies to either absorb the extra expenses or pass them on to customers, leading to higher prices for automated systems.
2. Supply Chain Disruptions
Tariffs can disrupt global supply chains by making certain suppliers less competitive. Companies that depend on just-in-time manufacturing may struggle with delays and shortages if they must switch suppliers due to tariff-related cost increases. This can slow down automation adoption as businesses face uncertainty in sourcing critical components.
3. Slowdown in Automation Adoption
Small and medium-sized enterprises (SMEs) that are considering automation may delay investments due to higher costs from tariffs. This could slow overall productivity growth in manufacturing, as automation is a key driver of efficiency.
4. Encouragement of Domestic Production
On the positive side, tariffs may incentivize companies to produce automation components locally. Countries imposing tariffs often aim to boost domestic manufacturing, which could lead to increased investment in homegrown automation technologies. However, building a competitive local supply chain takes time and may not immediately offset the negative effects of tariffs.
5. Trade Wars and Long-Term Uncertainty
Ongoing trade tensions, such as those between the U.S. and China, create uncertainty for automation suppliers and manufacturers. Companies may hesitate to make long-term investments in automation if trade policies remain unpredictable.
Are There Advantages to Tariffs?
While tariffs are generally looked down upon for their disruption to the flow in the global economy. When used responsibly and with proper domestic infrastructure in place, tariffs do have certain advantages.
Reshoring of Manufacturing
Companies may bring production back to domestic markets, increasing demand for localized automation solutions.
Innovation in Alternative Technologies
Higher costs for imported components could accelerate the development of new automation technologies that rely less on tariff-affected parts.
Strategic Sourcing Diversification
Businesses may seek suppliers in countries not subject to tariffs, leading to a more resilient supply chain.
Conclusion
Tariffs can present obstacles and potential opportunities for industrial automation. While they raise costs and disrupt supply chains, they may also encourage domestic production and innovation. Companies in the automation sector must adapt by diversifying suppliers, investing in local manufacturing, and exploring new technologies to mitigate risks. Policymakers should also consider their long-term impacts on industrial competitiveness, ensuring that trade policies support—rather than hinder—technological advancement.
As automation continues to transform manufacturing, navigating trade-related challenges will be crucial for sustaining growth and maintaining a competitive edge in the global market.
Are You In Need of A Replacement Drive?
Tariffs may present themselves as an obstacle, but don’t let a broken drive or motor slow you down. Do you need to replace your drive quickly and efficiently? Let our team of experts help you get your operation back up and running.