A Distributed Control System (DCS) is a type of automated industrial control system (ICS) used to control geographically distributed processes, such as those in factories, power plants, and other large industrial settings. DCS systems rely on a network of controllers distributed across a facility, allowing for real-time monitoring and control of multiple processes simultaneously. These systems are integral in industries where precise, continuous control is essential. Read on to learn more about the meaning of DCS.
What is a DCS?
A Distributed Control System (DCS) is a computerized control system that streamlines the functionalities of industrial devices used throughout a workspace. A DCS utilizes a wide range of controllers to permit all the parts to converse with one another just as PCs do. These controllers are distributed geographically across a plant to allow for high-speed communication to the control process. When utilizing various kinds of modules, the framework may require diverse correspondence norms, for example, Modbus and Profibus.
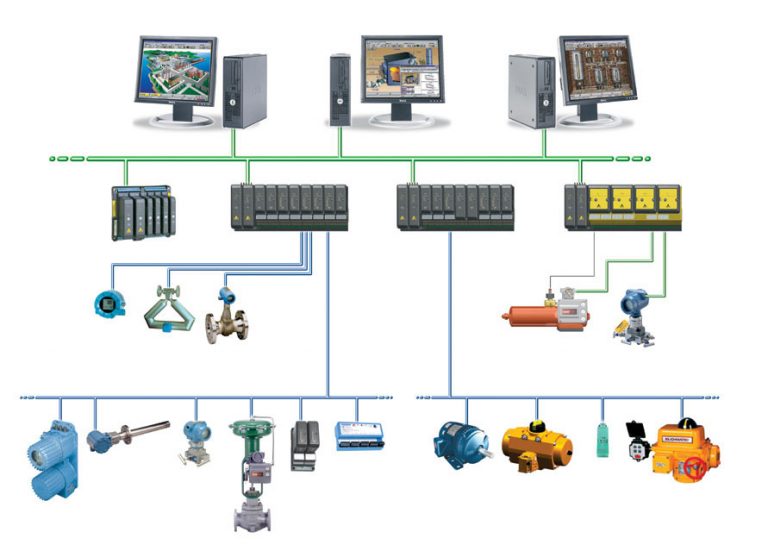