In a world full of misinformation and misconception, people tend to overlook one bit of knowledge. This specific misinformation manifests in the form of two specific objects, commonly found at home and at work. These objects hide under your bed. They lie forgotten about in the crevice behind your office desk. Heck! You may even find two to three of them daisy-chained together by some rabbel-rouser rebelling against OSHA!
Of course, I am talking about power strip and surge protectors. At a glance they both look and function in a similar way. However, once you get the past the surface level similarities, the differences begin to reveal themselves. At this point the importance of knowing the difference becomes very clear.
History
Power Strip
The history of the power strip traces back to the early 20th century. The increase demand for electricity in homes and workplaces made it necessary to have a way to power more devices. The earliest patent for a power strip dates back to 1929. As more electronic devices and appliances became integral to daily life, the need for additional electrical outlets became apparent. The earliest power strips were simple extensions of existing electrical wiring. They offered a convenient way to power multiple devices from a single wall outlet. These early versions were rudimentary, often lacking safety features and surge protection.
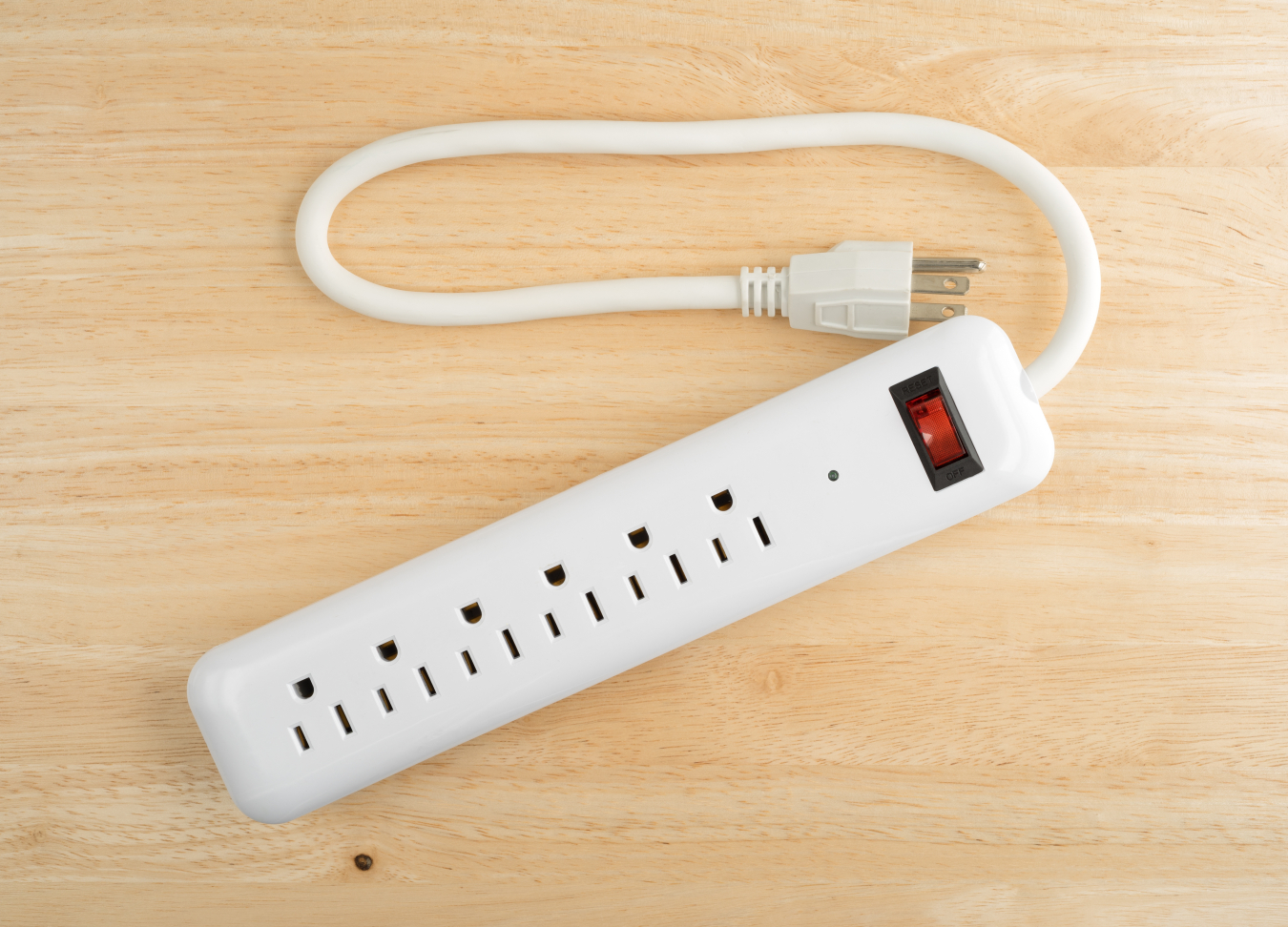
Advancements in electrical engineering led to the integration of safety features. These included circuit breakers and individual switches for each outlet. The 1970s saw the update and release of the power strip type that we all know today. With the rise of computers, home entertainment systems, and an increasing number of electronic gadgets, power strips became ubiquitous in households and offices. They played a pivotal role in managing the complex web of cords. They also provided a centralized power source for various devices. Power strips continue to evolve, incorporating smart technologies and energy-efficient designs.
Surge Protector
As more sensitive electronic equipment like computers and televisions became commonplace, the vulnerability of these devices became evident. Surge protectors emerged as a response to this challenge, aiming to mitigate the risks associated with power fluctuations. Early surge protectors were rudimentary. They often utilized devices like metal oxide varistors (MOVs) to redirect excess voltage away from connected devices. However, these early models lacked the sophistication and comprehensive protection features seen in modern surge protectors.
As technology advanced and electronic devices became more intricate and expensive, surge protectors evolved to offer enhanced protective mechanisms. Throughout the latter half of the 20th century and into the 21st century, surge protectors integrated advanced technologies, such as transient voltage suppressors and thermal fuses, to provide more robust defense against power surges. The growing awareness of the importance of surge protection has led to the widespread adoption of surge protectors in homes, offices, and industrial settings. Today’s surge protectors not only shield devices from voltage spikes. They also often include additional features like USB ports and smart functionalities to meet the diverse needs of contemporary users.
So What’s the Difference?
As mentioned above, at an initial glance power strips and surge protectors may seem like interchangeable jargon for the same item. However, the difference between them lies in their functionality and purpose. Power strips function as a tool for allowing power to multiple devices at once. The modern conception used today comprises of a multi-outlet strip with a power switch installed. Power strips serve multitude of uses across various industries. Shops utilize them for being able to use multiple power tools at the same time. Offices use them to hook multiple computer components. In the home they are often found in the living room powering the entire family entertainment system.
While the surge protector essentially finds itself used in the same way that the power strip does. Unlike the power strip, the surge protector has the added bonus of being able to actually protect devices if there is a voltage spike. Often these spikes (more commonly referred to as surges) come from things lightning strikes or power outages. It is often advised that all expensive and sensitive devices be connected to a surge protector as to ensure their longevity.
Conclusion
Understanding the disparity between power strips and surge protectors is vital for making informed decisions about the safety of your electronic devices. While power strips offer convenience, surge protectors provide essential protection against unexpected voltage fluctuations, ensuring the longevity and functionality of your valuable electronics. Finally, if you are trying to buy a surge protector make sure to read the box fully to ensure you are not buying a power strip.