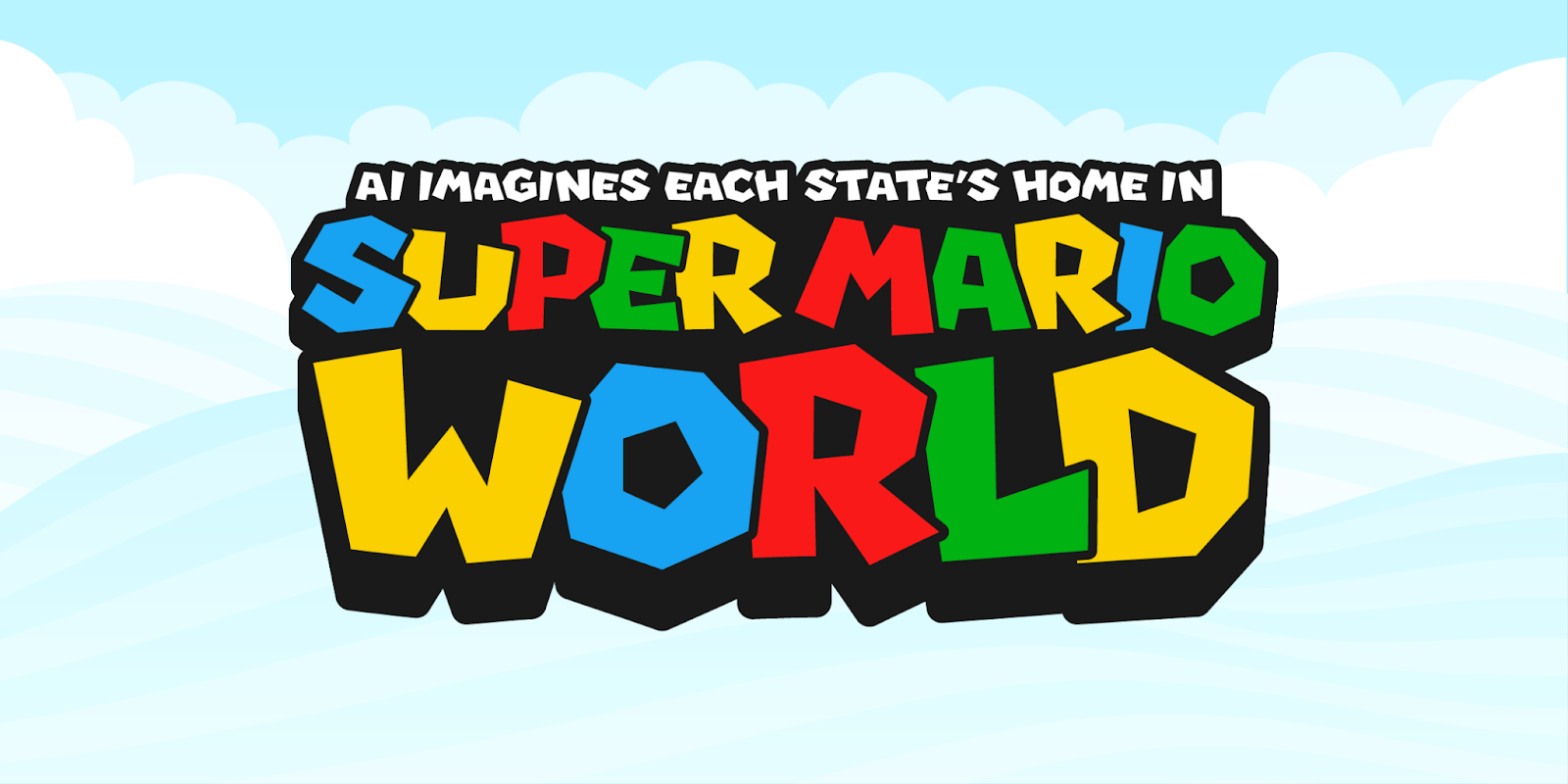
It’s-a me, MRO! As one of the most beloved video game franchises of all time, Super Mario has made us all wonder what life would be like in a world as unique and fun as Mario’s. Since we’re always exploring the capabilities of automation and AI at MRO Electric, we wanted to bring these thoughts to life with an AI image generator.
To discover if your state’s home would be more like Toad’s House or Peach’s Castle, check out the carousel of images below. Here we go!
Methodology
We asked ChatGPT to determine which Super Mario games and locations would best suit each state based on themes and brands associated with their geography and culture. From there, we prompted Midjourney with the relevant locations, games, and most popular home design styles in each state to visualize what their homes would look like in Super Mario’s world.
AI Reimagines Every State’s Home in Super Mario’s Style
Mario time! Across the country, many home images visually reference the art style of “Super Mario 64.” From the bold colors to the detailed landscapes, this Mario game seems to represent from coast to coast. Additionally, as you scroll, you will see that the AI slipped in Toad’s bright red mushrooms throughout, solidifying the classic red shroom as one of Mario’s most iconic symbols.
In classic Mario fashion, it’s all about the castles. Many homes have tall towers and gorgeous windows overlooking the lush plants leading up to the door. Finally, the classic blocky platforms that make the Super Mario games what they are can be seen in the walkways and the base of many homes.
Arkansas: Daisy’s Castle in Greek Revival Style
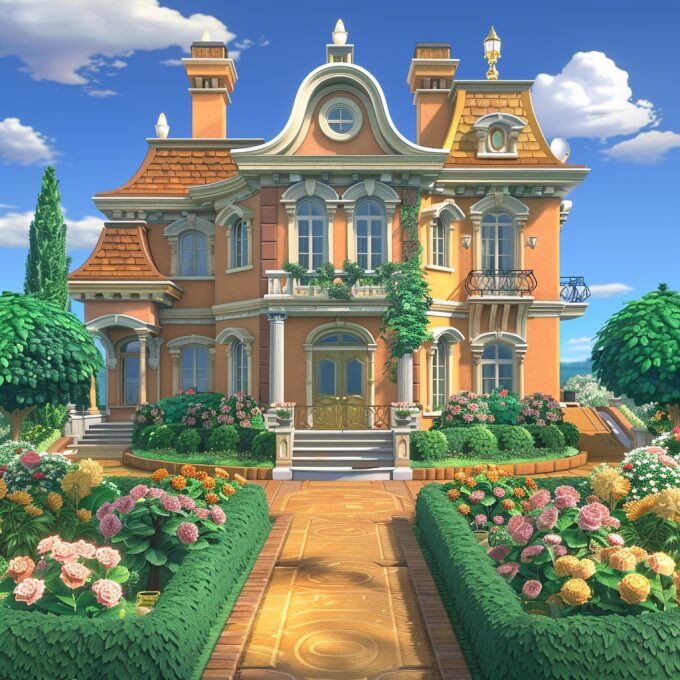
Arkansas’s home looks very similar to Daisy’s Castle with its orange and yellow theme. There is a clear reference to Peach’s best friend between the arches, towers, and golden doors. There’s even a blooming garden to match her floral namesake! This home’s architecture is based on the Greek Revival style popular in Arkansas, and it can be seen in the columns before the doors. Maybe Arkansans should consider changing their state flower from an apple blossom to a daisy!
Florida: Renaming the Gulf Coast to Peach Beach
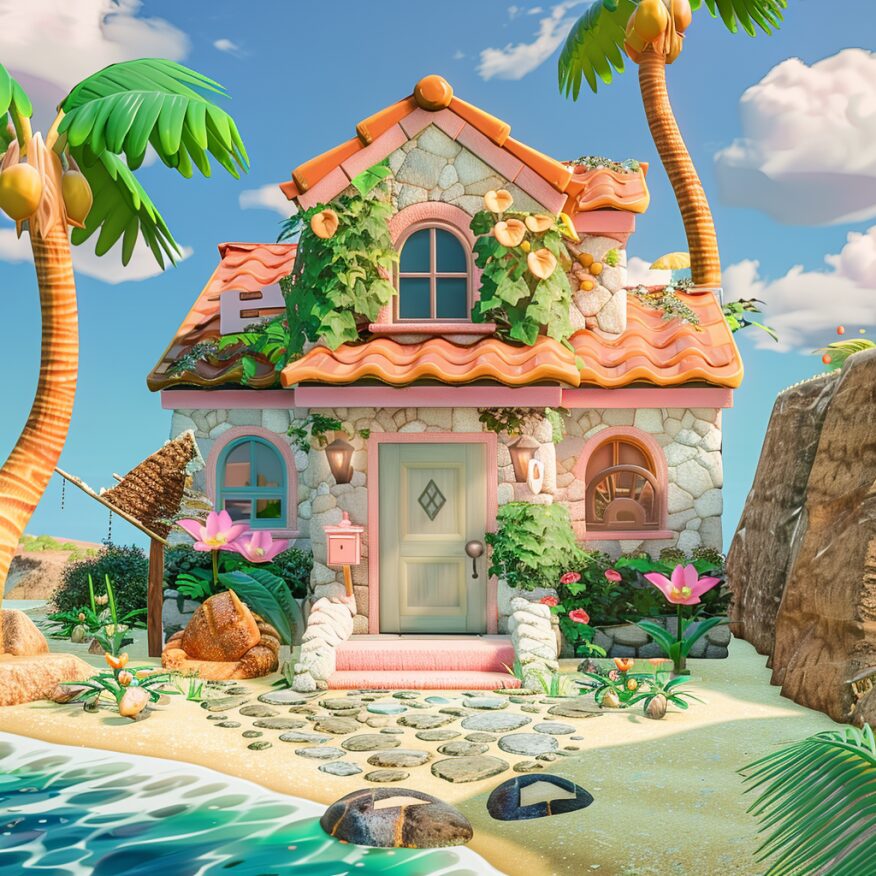
Let’s go to the Peach Beach! This setting resembles Peach Beach from “Mario Kart: Double Dash!!” with its faded Y2K colors and palm trees. It also references Peach’s style with the pink flowers and accents. The roof looks like it was made from a shell, which is a nice touch. This house could plop down on the Gulf Coast anytime!
Michigan: Arts and Crafts Style Meets Mushroom Kingdom
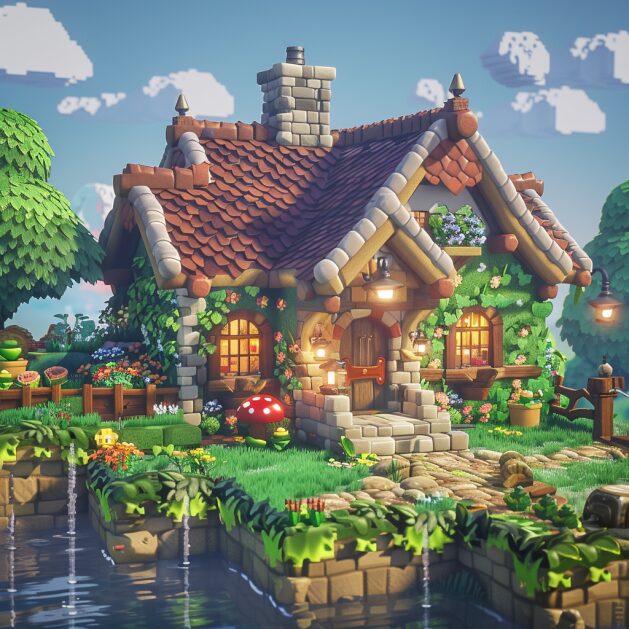
This image pulls from the New Super Mario Bros style of games with cleaner lines and brighter details, especially with the blocky path that would possibly require a double-jump to get up to. Being the Great Lakes State, this home’s landscape references both the Lake Kingdom and Mushroom Kingdom and the Arts and Crafts style of home depicted is one commonly seen in Michigan. Perhaps a home Mario would have to stop by on his way to save Peach!
Ohio: Industrial Lofts in Toad’s Factory
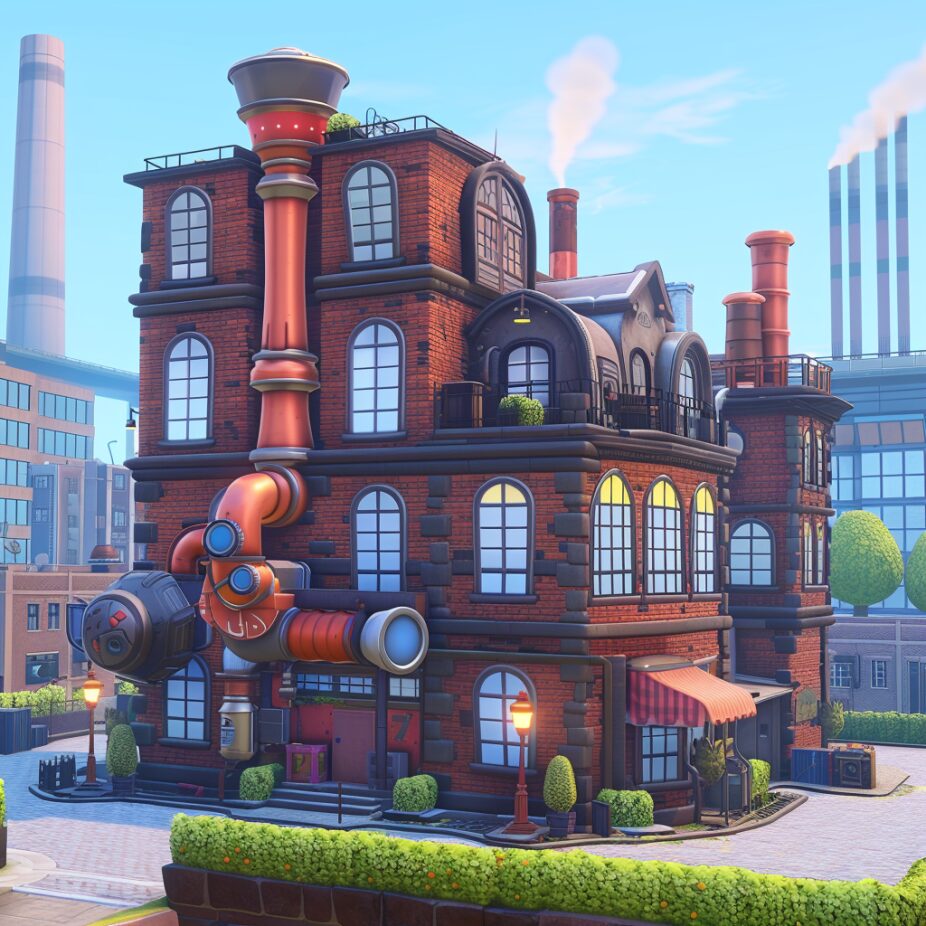
For Ohio, the AI is pulling from Rust Belt imagery here with the industrial loft homestyle. The art style is much more modern, with the twisting pipes and red accents on a city block. This must be what Toad’s Factory from Mario Kart Wii would look like if it were mixed with New Donk City of Super Mario Odyssey. Downtown Cleveland, watch out!
Wisconsin: Victorian Home or Luigi’s Mansion?
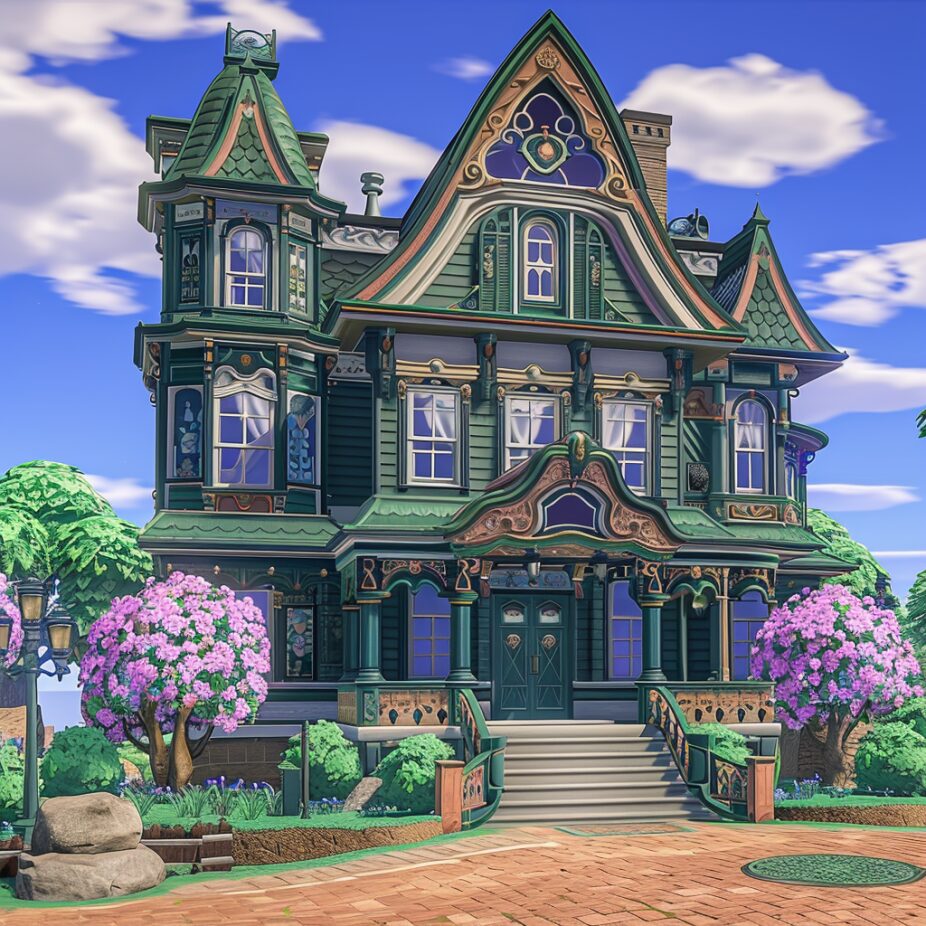
This Victorian home in Wisconsin resembles closely to Luigi’s Mansion. Who knew that Luigi is a Cheesehead? It follows Luigi’s style with the green base and purple highlights, as well as the style of his mansion with several stories, windows, and towers. One of the most spectacular references is how the furniture looks covered by a white cloth in the leftmost second-floor window. In Luigi’s mansion, that’s a very common, and spooky, decor choice. As beautiful as this home is, don’t forget that Luigi’s Mansion is haunted!
Closing Thoughts
In addition to the whimsical characters and power-ups, Super Mario’s world is filled with advanced technologies and mechanics. With a supply of innovative products and forward-thinking manufacturers, our team at MRO Electric helps distribute and repair the tools needed to make the world just as cutting-edge and imaginative as AI’s depiction of homes in Super Mario’s world.