When replacing a Fanuc A06B-6050-H103 Servo unit you should check to make sure the replacement servo has the same top board, part number A20B-1000-0560. After this part number there will be a “/” and then something similar to “05A” which denotes the revision of the board. Ideally you would match your original unit with a replacement unit that has the same board, but if that’s not possible then all you would need to do is reconfigure the jumpers on the board. The table below shows how to get this set up so you can get your servo back up and running right away. Search for more FANUC motors/drives on our website.
Fanuc Alarm 466 – Z Axis: Motor/Amp Combination
We just shipped out a Fanuc A06B-6096-H207 Servo Amp unit to a customer, and as soon as they installed the amplifier they got a Fanuc Alarm 466 which refers to the Z Axis: Motor/Amp Combination. This is obviously somewhat distressing for a customer to buy a replacement unit and immediately get an alarm when it is installed, but fortunately this is an easy fix.
This Alarm 466 comes from the replacement amplifier having newer servo software than the unit that it is replacing. As Fanuc has made newer units they’ve upgraded the software/hardware within these amplifiers, so you just need to reset a parameter to reboot the configuration and clear the 466 Alarm. The steps are below.
– Put the machine in Emergency Stop
– Go to parameter 2165 on the control
– Set all the values to 0
– Take the machine out of emergency stop
Once these parameters are changed and the machine is rebooted, the alarm will clear and the amplifier will initialize. We also have pictures below to confirm that you know what to look for. For any additional help, call us at 800-691-8511 or email sales@mroelectric.com.
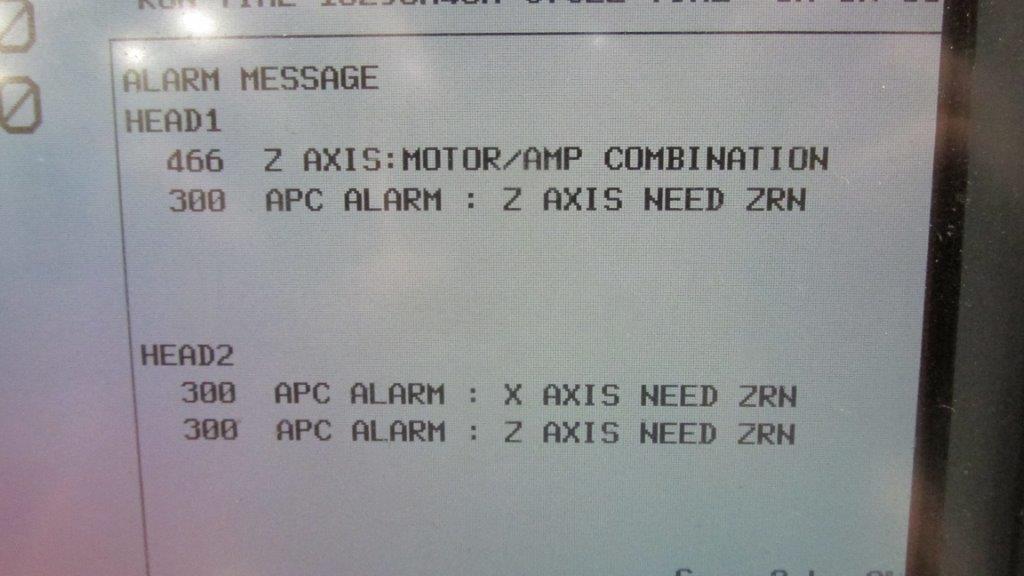
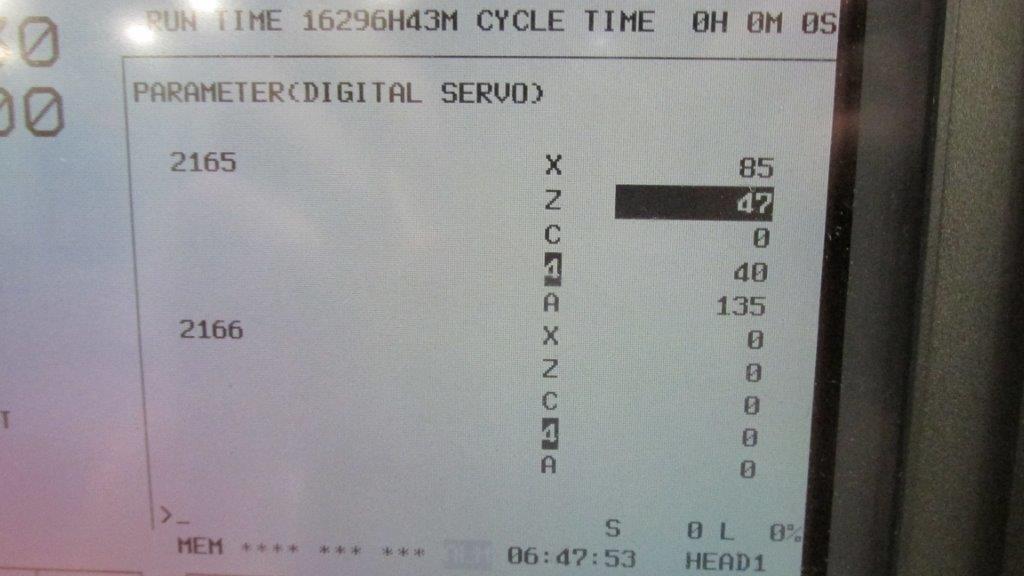
MRO Electric stocks a large number of FANUC CNC Products, and provides repair services as well. For more information or to request a quote, please call 800-691-8511 or email sales@mroelectric.com.
Simodrive E/R Module Fault – Troubleshooting
We had a customer who was getting an alarm on their Simodrive E/R Module with a fault on the machine after the hydraulic was put on. They had tried resetting the machine but the same alarm would come back up. The Simodrive part number was 6SN1145-1BA01-0DA1, the only light on it was the green LED and the terminals were both reading 27VDC. The customer was considering buying a new drive but wanted to check to see if there was some way of resolving the issue without buying a whole new Simodrive.
Based off the LED configuration that the customer was having, we determined that the external enable signal 63 was missing, so they needed to double check their connections. When the customer checked, the contact from the hydraulic connector was not making a good connection. All the customer needed to do was replace the contact kit and restart the machine which got them up and running. We would highly recommend always double checking the connections on a unit before replacing it, because there can often be a simple issue that doesn’t require the full unit to be replaced.
Contact MRO Electric and Supply at (800)691-8511 or email us at sales@mroelectric.com about repair services.
Simodrive Repair Service
We know that downtime is crippling for all of our customers, which is why we stock almost all of our inventory to be ready to ship overnight to a customer or even be couriered in. Still, there are some times when even we don’t have the part you need in stock, or you just want to save some money, so this is why we offer repair on your existing parts. One of our main repair capabilities is for Siemens Simodrives. Our Simodrive Repair Service has a turnaround time of 3-5 days, and we are even able to get some repairs done sooner. All of our repairs come with a 1 year warranty and are fully tested before shipping back out.
MRO Electric and Supply maintains a comprehensive stock of new and used FANUC CNC and FANUC Robots parts, Siemens parts, Yaskawa parts, etc. If you need a FANUC replacement part, please call 800-691-8511 or email sales@mroelectric.com.
372SPU47401V26 Concept XL Software – Product Video
Below is a video of the 372SPU47401V26 Concept XL Software which is use for programming Schneider Electric PLCs. This package comes with the discs and license to install 1 work stations with this Concept software. This software can be used to program Modicon Compact (service only), Modicon Momentum, and Modicon Quantum. It can be used on MS Windows XP, Windows Vista, and Windows 2000. We have this software in stock, for more product info email sales@mroelectric.com or call 800-691-8511.
6FC5210-0DF22-2AA0 Siemens PCU – Product Video
Below is a product video for a 6FC5210-0DF22-2AA0 Siemens PCU unit which we have in stock and ready to ship. This is a Siemens control unit with software set to run a CNC system. We have a video showing the booting up of a similar PCU 50 Siemens unit on a blog post here where we show one of these units powering up. They are basically a computer with an operating system loaded on that you can hook up to a display, keyboard, and mouse to get booted up and programming your system. Visit MRO Electric and Supply’s website for more parts from Siemens. For any questions email sales@mroelectric.com or call 800-691-8511.
Siemens 6SN1118-0DJ23-0AA0 Control Card – Product Video
Here is a video of one of the Siemens 6SN1118-0DJ23-0AA0 Control Cards that we have in stock. This is a control card for a Siemens Simodrive system, and would be inserted into a Simodrive power module such as a 6SN1123-1AA00-0EA1. We occasionally have people call in to order just the control card or just the power module, not realizing that they are two separate units that are sold separately. When deciding that you have an issue with one of these, make sure you test both the power module and the control card and order accordingly. The control cards can be used in multiple power modules so there is not one particular setup for installing one of these. If you are replacing the control card, you should also test the power module before replacing the control card because you can end up damaging the replacement 6SN1118-0DJ23-0AA0 control card if it is installed in a faulty power module.
The 6SN1118-0DJ23-0AA0 unit in this video has been fully refurbished, retested, and repackaged in our own packaging. We have plenty of all of the different Simodrive control cards in stock, so if you’re looking for a similar unit just give us a call at 800-691-8511 or email sales@mroelectric.com for a quote. The individual parts page for this unit is here, hopefully this helps and if you need anything else please let us know.