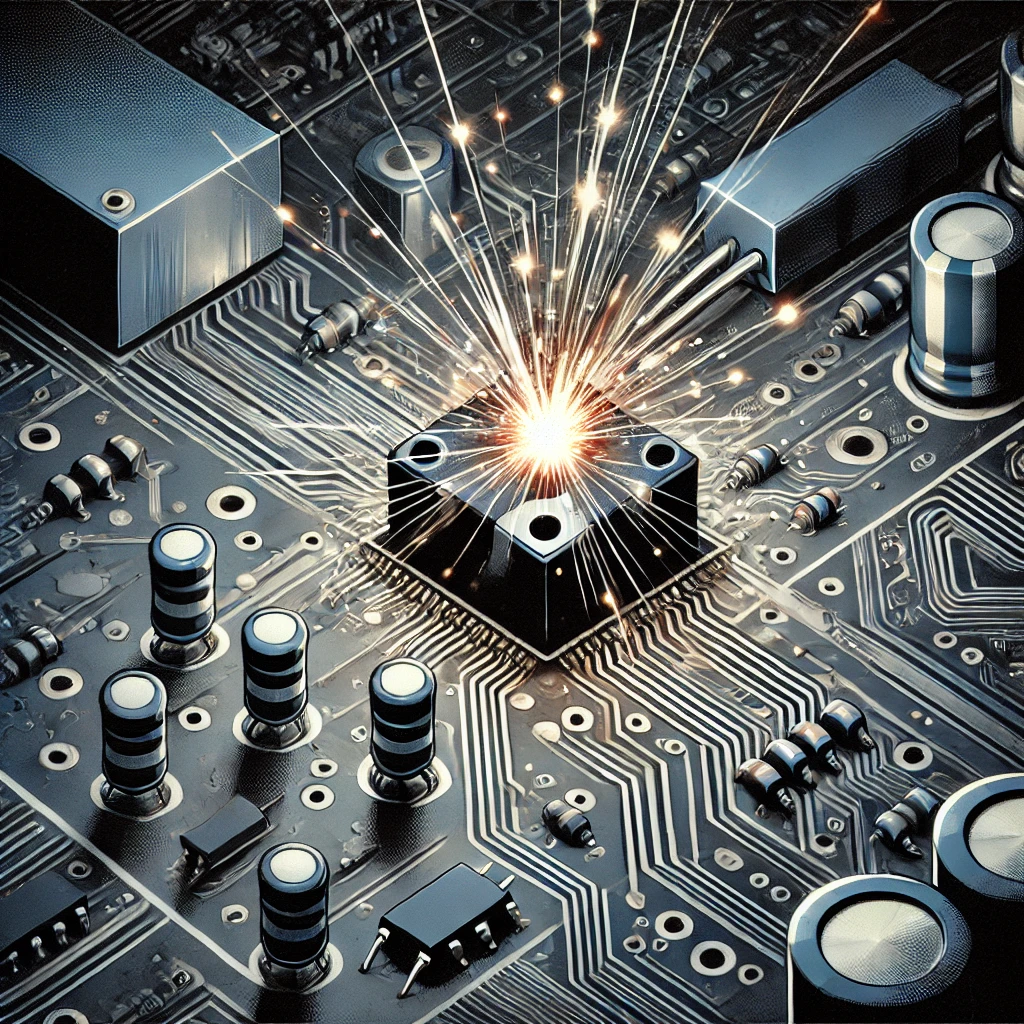
Understanding an Arc Flash
An arc flash stand as one of the most dangerous electrical hazards encountered in industrial settings. They occur when an electrical current travels through the air between two conductive points, creating an intense burst of heat and light. This sudden, high-temperature discharge of energy can cause severe injury, damage equipment, and even lead to fatalities. While seemingly a rare event, arc flashes occur more than many realize. The consequences if we ignore proper precautions end up being catastrophic.
The energy released during an arc flash can reach temperatures as high as 35,000°F, which is four times the surface temperature of the sun. This extreme heat can vaporize metals like copper and steel, causing molten metal particles to fly through the air. The accompanying pressure wave from the rapid expansion of air can also result in physical injuries, such as hearing damage, lung damage, and blunt-force trauma from projectiles. Additionally, the bright light produced can lead to temporary or permanent blindness. The sheer intensity of them is why it is so critical to understand the risks involved.
Read more: Understanding an Arc FlashWhat Causes an Arc Flash?
Several factors can cause an arc flash. These include equipment failure, improper installation, faulty maintenance, or human error. For instance, using improperly rated or damaged tools, dropping metal objects near live equipment, or working on energized systems without proper safety gear can all result in an arc flash. Even something as simple as dust or corrosion on electrical equipment can lower insulation resistance, allowing an arc to form. The likelihood of these events increases significantly in high-voltage environments. Electrical substations or industrial plants that store and manage large amounts of energy daily, often see the highest risk.
The Dangers of an Arc Flash
An arc flash can lead to significant damage to equipment, causing costly downtime and repairs. High-energy ones can destroy electrical panels, cables, and machinery, resulting in production delays and expensive replacements. Worse, if an arc flash ignites nearby flammable materials, it could trigger secondary fires, further escalating the damage. Therefore, many companies invest in preventative measures like sophisticated detection systems and remote operation technology, which allow workers to interact with electrical equipment from a safe distance.
How to Protect Your Equipment
Preventing arc flash incidents starts with the proper training and education of personnel working in environments with electrical systems. Workers need thorough training on how to understand the hazards of arc flashes. The should also know how to identify risks, and the correct safety procedures to follow. One of the most effective preventive measures is to always de-energize electrical equipment before performing any maintenance or repairs. Lockout/tagout (LOTO) procedures, which involve isolating the energy source and placing a lock on the equipment to prevent accidental re-energization, are crucial to minimizing the risk of ocurrences.
Another key precaution is the use of appropriate personal protective equipment (PPE). Workers exposed to potential arc flash hazards should wear flame-resistant (FR) clothing, gloves, and face shields that meet the arc rating required for the specific electrical task. This gear can withstand the high temperatures and energy released during an arc flash which significantly reduces the severity of injuries. Additionally, using safety tools, such as insulated hand tools, reduces the likelihood of accidental contact with live components. It’s also important to maintain a safe working distance from energized equipment, especially in high-voltage environments.
Lastly, routine inspection and maintenance of electrical systems are vital in preventing arc flash incidents. Equipment should be regularly checked for signs of wear, damage, or corrosion, which could compromise insulation and increase the risk of an arc flash. Faulty components should be repaired or replaced promptly. Implementing arc-flash detection and mitigation systems can further reduce risks by automatically shutting down electrical systems if dangerous conditions are detected. By combining proper safety practices, equipment maintenance, and protective measures, companies can significantly lower the chance of arc flash events and protect both workers and equipment.
Conclusion
In conclusion, an arc flash is a potentially deadly hazard that demands respect and proper safety measures. Through a combination of education, awareness, and adherence to established safety protocols, the risks of incidents can be minimized. Understanding the causes, consequences, and prevention strategies not only ensures the safety of workers but also helps maintain operational efficiency and reduce the financial impact of equipment failure. Whether you’re an electrician, engineer, or plant manager, prioritizing arc flash safety is a non-negotiable part of protecting both people and infrastructure.
Damaged Part? Need a Replacement?
If you’re experiencing a damaged drive from an arc flash reach out to us! Our team of experts are ready to help you get your operation back up and running in no time. Our customer service team can be reached by email: sales@mroelectric.com or by phone: (800) 691-8511.
If you liked this article, you may enjoy our other article covering “dirty power” and its effects on industrial equipment.