The Siemens 6SN1123-1AA00-0CA2 is a Simodrive 611, 1 Axis Power Module. With the control module, the 6SN1123-1AA00-0CA2 forms the drive module for feed or main spindle applications. The module provides power to the control boards as well as the connected motors. It can be used to operate a variety of Siemens and 3rd party motors. This module is graded according to a certain rating and can be supplied with three different cooling techniques. The module is equipped with overload protection. When this is dimensioned properly, it prevents both the cables and motors from being overloaded. the power module has two operating modes – one for Feed drives and another for Main spindle drives.
The 6SN1123-1AA00-0CA2 can be used for a variety of solutions due to its modular and space saving attributes. The module’s output limits can be modified by the control module in use. The drive modules can be operated from both an unregulated and regulated supply modules belonging to the Simodrive 611 drive system. The power module draws its supply required to control the motors from the DC link.
Then installing a control board into the 6SN1123-1AA00-0CA2, make sure the following is observed:
- Ensure that the power module is in a no-voltage condition.
- Check that the memory module is inserted and locked into place in the control board.
- Insert the control board into the power module.
- Tighten the screws retaining the board (2 on front panel).
- Connect the front panel of the board corresponding with its applicable connection diagram. The mating connectors must be inserted at the appropriate interface.
MRO Electric stocks both new and refurbished 6SN1123-1AA00-0CA2 Power Modules. For more information or to request a quote, please call 800-691-6511 or email sales@mroelectric.com.
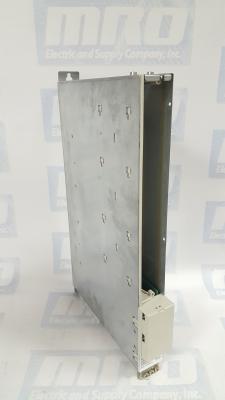