What could possibly make a sunny afternoon even sweeter? How about discovering what ice cream reigns supreme in each state across the USA? Whether it’s the rich swirl of chocolate, a classic scoop of vanilla, or something a bit more adventurous like lavender honey, every state has its favorite ice cream flavor and brand that keeps the locals lining up, even on the chilliest of days.
In this frosty feature, we’re diving scoop-first into the cool world of ice cream preferences across America. Using the latest Google search trends, we’ve churned out a list that’s sure to surprise and delight. So, grab your spoons (and maybe a napkin or two), and let’s embark on a creamy journey to uncover each state’s favorite ice cream. Who knows? You might just discover your new go-to along the way!
The Most Popular Ice Cream Flavor in Every U.S. State
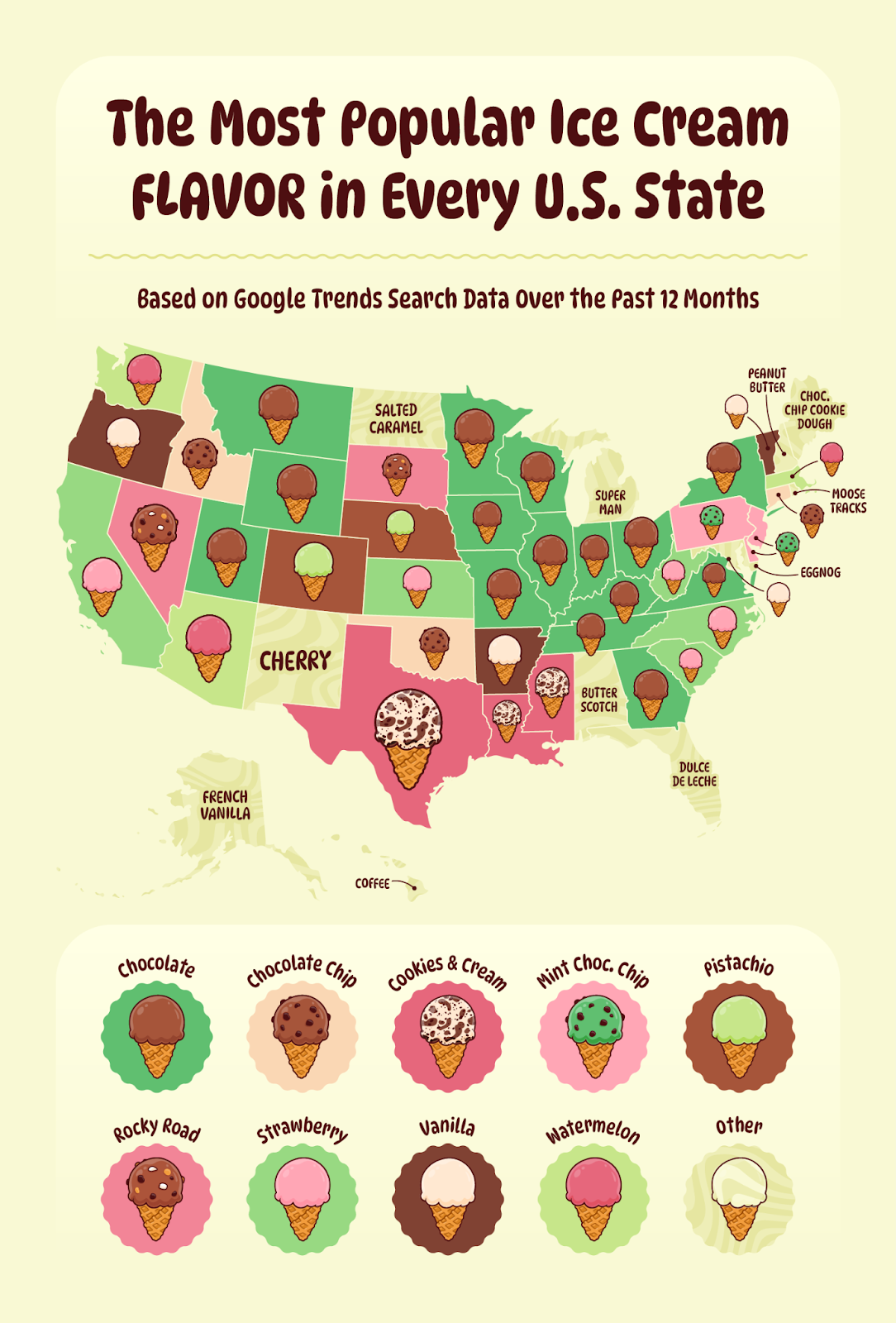
America has spoken, and the verdict is as sweet as it gets! At the top of the ice cream pyramid sits none other than the classic chocolate, capturing the hearts—and spoons—of 15 states. Is it the smooth, velvety texture or the deep, decadent flavor that has states such as Georgia, Kentucky, New York, Tennessee, Utah, and Wisconsin swooning? Whatever the reason, it’s clear that chocolate is the king of ice cream flavors in the U.S.
Strawberry swirls in at second place, painting five states –California, Kansas, North Carolina, South Carolina, and West Virginia– in its delightfully pink hue. This fruity favorite is more than just a summer fling; it’s a year-round love affair for those who prefer a tangy twist to their treat.
Trailing closely behind, and never out of style, is vanilla, claiming four states –Arkansas, District of Columbia, Oregon, and Vermont– as its territory. While some might call it plain, aficionados know better. Vanilla’s subtle sweetness and creamy consistency make it a versatile base that plays well with almost any topping, from hot fudge to fresh fruit. It’s the canvas of the ice cream world, allowing imaginations to run wild with flavor combinations.
Some states, however, are drawn to the less conventional flavors. Michiganers, for example, love to order up a scoop that’s known for its bright hues of blue, red, and yellow which give it its namesake after the iconic superhero: Superman. Moving towards the east coast, Rhode Island residents have a love for the indulgent Moose Tracks– a scoop that typically consists of vanilla ice cream with added elements of chocolate fudge and peanut butter cups!
So, whether you’re a devotee of the rich and chocolaty, a fan of the fruity and fresh, or a purist who prefers the understated elegance of vanilla, there’s a flavor on this map for everyone. While each state’s preference may vary, our love for this frozen delight is a common thread that binds.
The Most Popular Ice Cream Brand in Every U.S. State
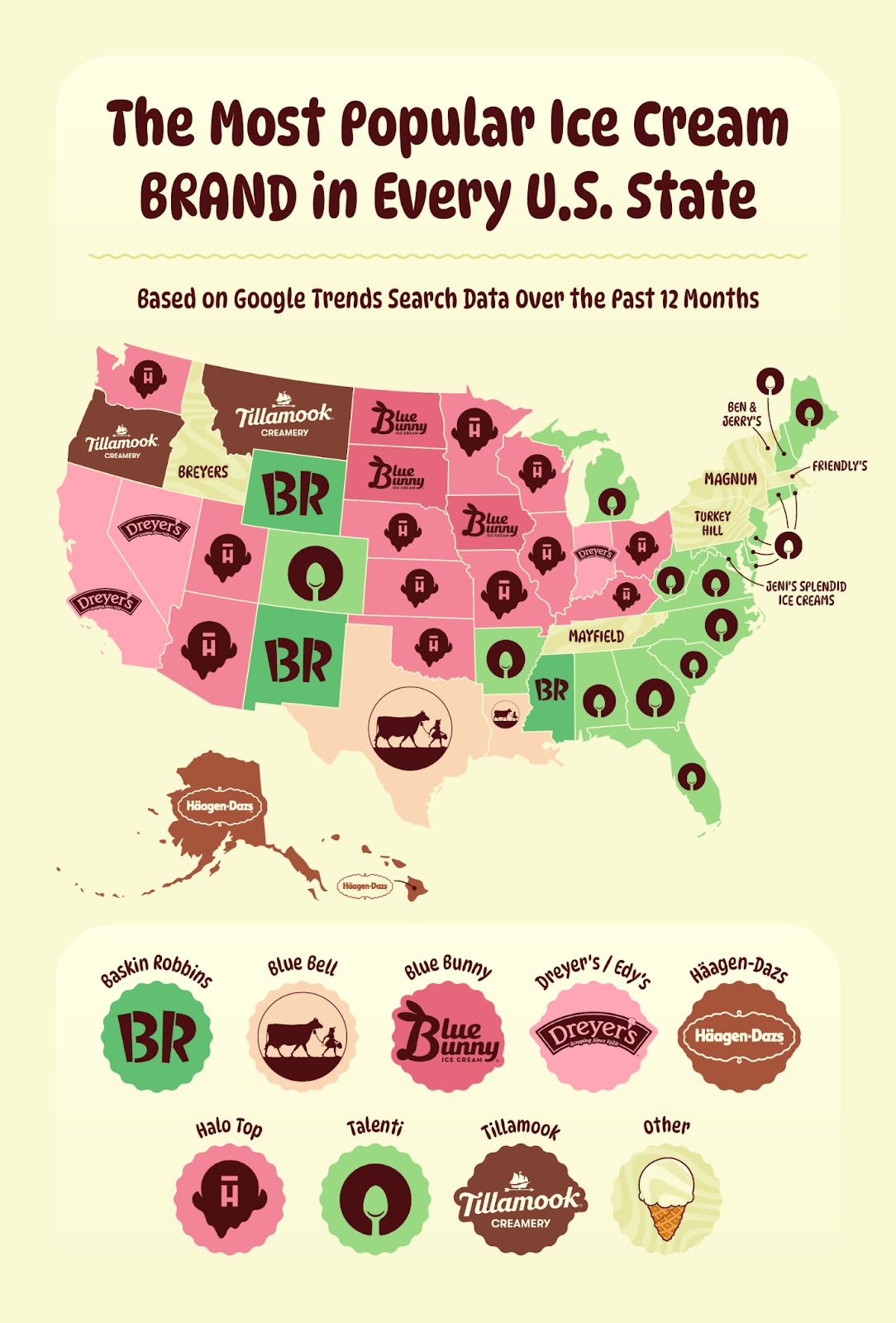
When it comes to ice cream brands, it seems America has found a true gem in Talenti. This beloved brand scoops its way to the top as the most popular choice in 17 states, winning hearts with its artisanal approach. Known for its rich, creamy texture and a wide array of innovative flavors, Talenti has become a household name from coast to coast. Whether it’s the smoothness of their Mediterranean Mint or the decadence of their Sea Salt Caramel, Talenti has a knack for turning every pint into a gourmet experience.
Hot on Talenti’s heels is the health-conscious yet indulgent Halo Top, the favorite in 12 states. This brand has managed to bridge the gap between indulgence and wellness, offering a low-calorie option that doesn’t skimp on flavor. With classic flavors like Birthday Cake and Peanut Butter Cup, it’s no wonder Halo Top has amassed a loyal following.
In a three-way tie for third place, we find the timeless classics: Baskin Robbins, Blue Bunny, and Dreyer’s (or Edy’s, depending on which side of the Rockies you reside). Baskin Robbins, with its iconic 31 flavors, continues to be a favorite for those who love variety and nostalgia. Blue Bunny, celebrated for its fun and playful approach to ice cream, delights fans with flavors that are as whimsical as they are delicious. And Edy’s/Dreyer’s offers a comforting range of family-friendly favorites that have been staples in American freezers for generations.
America’s top ice cream brands reflect a diverse palate that caters to every craving. Whether you’re a fan of the gourmet, the healthy, or the timeless, there’s an ice cream brand out there ready to make your day a little sweeter.
Closing Thoughts
From the most popular ice cream flavors to the top brands, this delicious treat is a universal joy that brings people together and adds a touch of delight to our days. Whether it’s the rich indulgence of chocolate, the fruity freshness of strawberry, or the classic appeal of vanilla, each state has its own unique favorite that has carved out a special place in the hearts (and freezers) of Americans. Just as MRO Electric services are essential to keeping your business running smoothly throughout the year, ice cream is the sweet fuel that helps us all power through the hot summer months. So, let’s raise our cones to a tour of America’s favorite ice cream—it’s been a delicious ride!
Methodology
To find out which type of ice cream flavor and brand were the most popular in each state, we compiled a list of commonly eaten ice cream across the U.S. by looking at 29 ice cream flavor keywords and 16 ice cream brand keywords on Google Trends from June 2023 to 2024.