Like many things in life, Fanuc servo amplifiers are not a one size fits all situation. Different servo amplifier models appropriately fill the roles of different scales of operation. You have to consider not only the cost of the amplifier, but also how well does it fit the needs of your operation.
Read more: Finding the Right Fanuc Servo Amplifier
Fanuc, a leading manufacturer of CNC systems and automation technologies, offers a wide range of amplifiers designed to control servo and spindle motors in industrial machinery. These amplifiers play integral roles to the precise operation of CNC machines. They fall into categories based on their capabilities, applications, and technological advancements. Below is an overview of the different series of Fanuc amplifiers:
Alpha i-D Series
FANUC’s new generation amplifiers have a smaller footprint, needing up to 30% less space than previous models. With an expanded multi-axis amplifier lineup, this series of drives saves energy use through its new low-consumption design as well as reduced fan operation. A brake control circuit is integrated into the servo amplifiers and a Leakage Detection Function is available in all Alpha i-Ds. Plus, an easy fan replacement feature makes these drives a breeze to maintain. The Alpha i-D Series Amplifiers can be connected to current FANUC CNC Plus Series models.
- Features:
- Integrated power supply and servo modules.
- Compact design for space-saving installation.
- High-speed communication with CNC systems.
- Compatible with a wide range of Fanuc motors.
- Applications:
- General-purpose CNC machines, such as lathes and milling machines.
- Suitable for both small and large-scale industrial operations.
Alpha i Series
The Alpha i series is an upgraded version of the Alpha series, offering enhanced efficiency and more advanced features.
- Features:
- High-efficiency power modules reduce energy consumption.
- Advanced diagnostics and monitoring capabilities.
- Support for multiple axis control in a single unit.
- Improved thermal management for longer service life.
- Applications:
- High-precision CNC machinery.
- Industries requiring energy-efficient operations.
Beta i Series
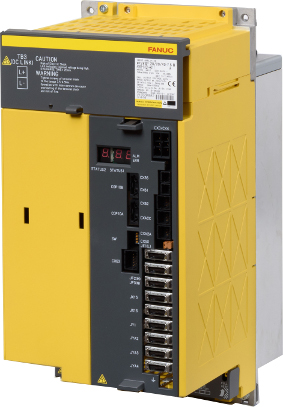
The Beta series amplifiers are designed for cost-effective operations without compromising on performance.
- Features:
- Simple design for easy installation and maintenance.
- Economical choice for smaller machines.
- Integrated power supply and servo amplifier units.
- User-friendly setup and configuration.
- Applications:
- Entry-level CNC machines.
- Compact machinery with moderate performance needs.
Spindle Amplifier Series
Fanuc’s spindle amplifiers are dedicated to driving spindle motors, which require high power and speed control.
- Features:
- High torque and speed control capabilities.
- Advanced thermal and power management.
- Integrated monitoring and diagnostics.
- Support for heavy-duty applications.
- Applications:
- High-speed milling and grinding machines.
- Heavy-duty lathes and turning centers.
What to Consider
Now that we’ve listed a selection of servo amplifiers that Fanuc has to offer, the question of “Well how do I know which to get?” arises. Before making that decision here are some things to consider that may be helpful.
- Machine Requirements
- What is the power, torque, and precision needs of your operation?
- Compatibility
- Make sure that the servo amplifier matches the CNC and motor in use.
- Scalability
- Is your system modular? Can it be scaled for future upgrades?
- Cost-Efficiency
- Does the long term gain and efficiency justify the initial cost?
Conclusion
Choosing there right servo amplifier can be a challenging task, but going through and observing the cost and benefit analysis of each series as well as the technical compatibility can make the process of getting a new servo amplifier a less frustrating experience.
Need a Fanuc Servo Amplifier?
To make your acquisition of a Fanuc servo amplifier an even easier experience, our team of experts can help you get connected with the right machine that suits your needs perfectly. Call: +18006918511 or email: sales@mroelectric.com