Low-code programming is an emerging trend promising to revolutionize software applications’ development and deployment. Utilizing visual modeling tools and pre-built components, low-code programming helps developers create and customize applications quickly and easily, without the need for extensive coding skills. Not only is it shaking up the world of software development, but it is making big splashes in the world of industrial automation. This is especially so when we talk about PLCs.
The Current Language of PLC
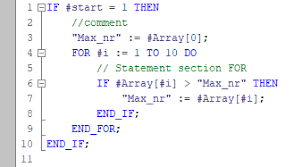
In another blog, we covered ladder logic. This is the primary coding language that PLCs use to function and perform tasks. Ladder logic is based on an older coding language known as C. Traditionally, coding in languages like C requires a mix of prompts formatted in very specific ways. This requires a well-versed coder programming the PLCs. The other challenge is not only that a person has to know the coding language, but also just be able to visualize how it all works together. Lines of code don’t always get along with each other. This sometimes results in an unexpected outcome not seen in the initial programming. This generally gets referred to as a “bug”. A good programmer must be one that can recognize, isolate, and debug what is causing these issues.
What is Low-Code Programming?
Low code is defined as a software development approach that requires little to no coding to build applications and processes. Instead of complex programming languages, it utilizes visual interfaces with basic logic and drag-and-drop capabilities in a development platform. This quick and simple alternative to conventional software development continues to grow in popularity.
Applying Low Code to PLC
While the trend of low code exists predominantly in the field of programming and development. It is also a concept being adapted to the field of industrial automation. More specifically, PLCs can adapt the low code model as traditionally they operate on a basic programming language.
The Advantages of Low-Code
There are several advantages to systems using a low-code environment. These advantages include faster times, better productivity, increased flexibility, and reduced costs.
With faster times, developers create applications much faster than traditional coding methods. They use pre-built components and visual modeling tools, to assemble and customize applications without the need for extensive coding.
Faster Times – Low coding allows PLC programmers to input programs much faster and not restricted by traditional coding methods.
Better Productivity – With less effort and time required than traditional programming, facilities can operate faster and more efficiently. An engineer can program a PLC much easier.
Increased flexibility – PLC programmers can quickly debug/modify the program of a PLC a lot easier than finding lines of code and rewriting them when the situation changes.
Low Cost – Low code programming will in the long run be less expensive, as unlike traditional programming, the PLC programmer does not need to have extensive knowledge of coding.
Future Outlook
Ultimately, the outlook for low code’s place in the world of industrial automation appears more prominent than ever. While there are concerns about how it will impact the future labor force. At its core low code serves as another example of automation making a specialized position obsolete. In the end, Low code’s multifaceted advantages of being flexible, quick, and cost-effective make it very appealing to companies across the industry, meaning that (for the time being at least) it’s here to stay.