You can check out our previous blog post on the UD75 here for more information. Check out the UD75 product page on our website along with all of our other Unidrive options.
UD75 Configuration
- Isolate the drive from the mains supply and allow 5 minutes for the DC Bus capacitors to discharge.
- Insert Large Option Module as shown below. Ensure that it is correctly inserted. The module will click firmly into place.
- To remove the module, pull on the black tab, and the module will disengage from the connector and pull out of the drive.
UD75 Configuration: Cable Screen
UD75 Configuration: Network Termination
For price and ordering info you can email sales@mroelectric.com or call 1-800-691-8511. We have these and all the other Control Techniques Unidrive Classic option modules in stock, along with the drives themselves.
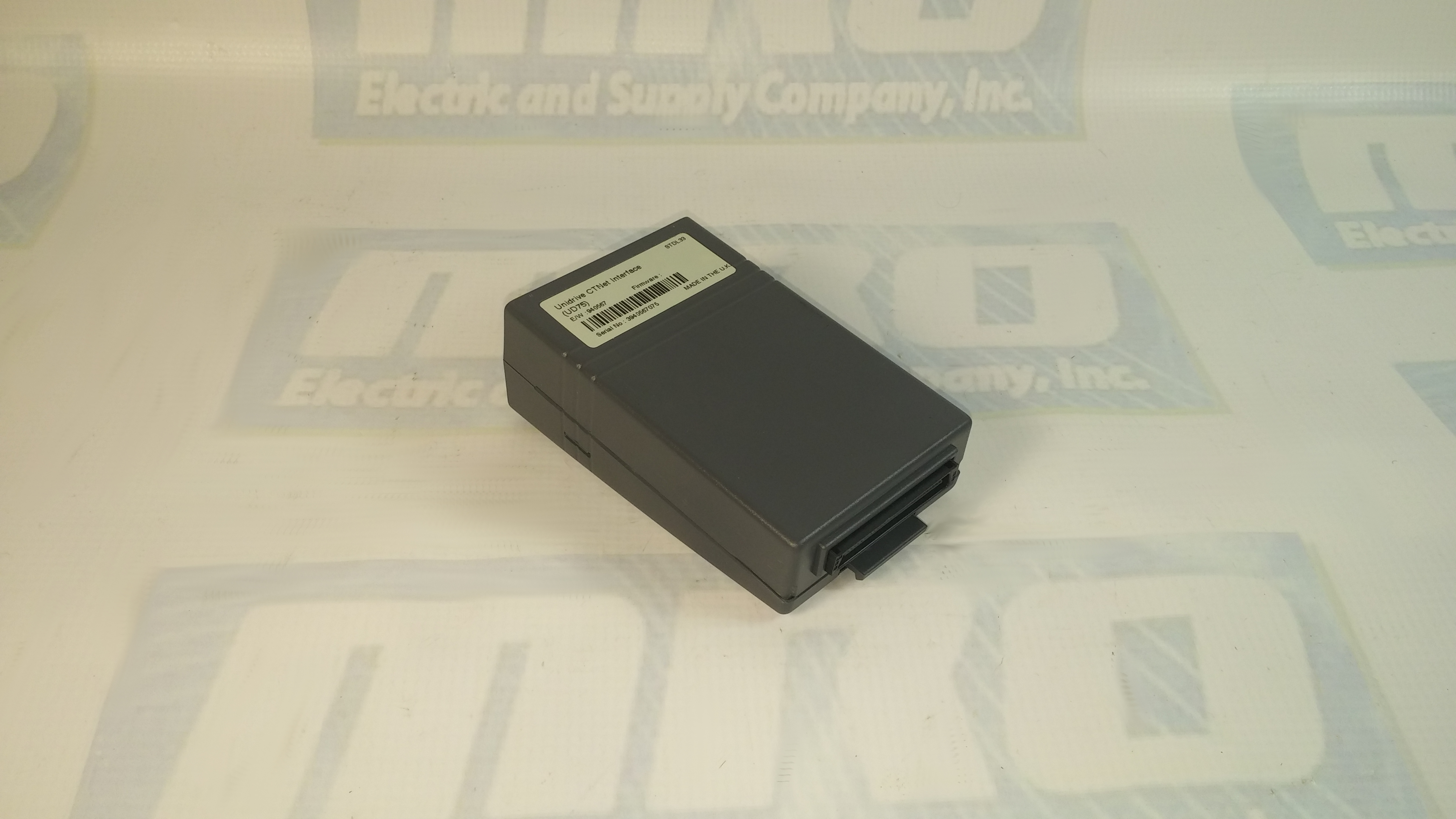