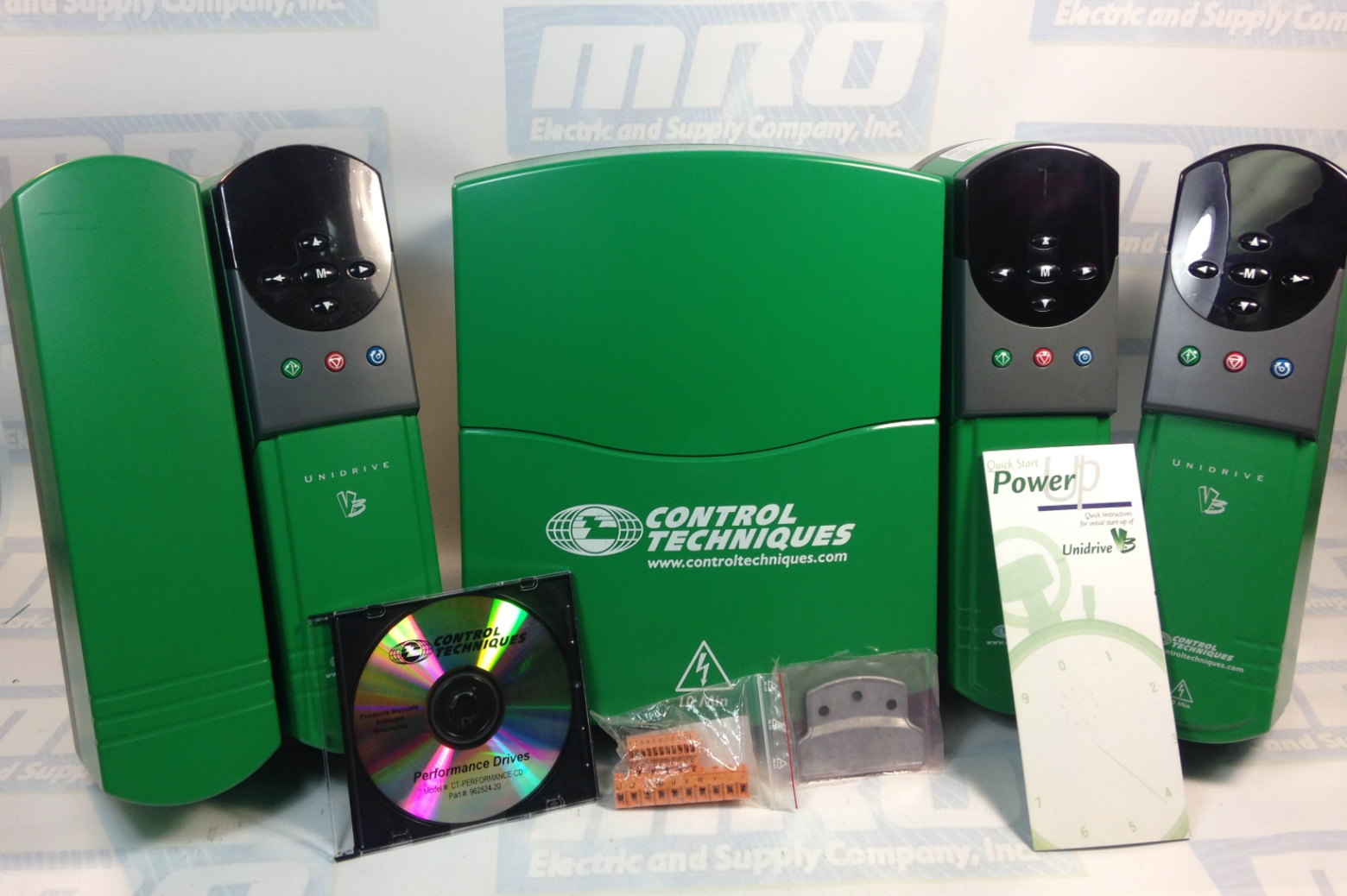
Unidrive Classic Option Module Trip Codes
On Unidrive Classics, when a UD7x Unidrive option module error trip occurs,
the display will show the trip code as “tr__”. The trip number
can also be read in Unidrive parameter #10.20 or UD70
virtual parameter #88.01, and the line number where the trip
occurs in parameter #17.03, though only if the program was
compiled with debugging information.
When an error occurs in the UD70, the DPL program will
immediately stop. Also, depending on the cause of the trip
and the setting of the Trip enable parameters, the Unidrive will
trip on the “tr__” code. Optionally, an ERROR task may have
been defined which would be executed whenever a run-time
error occurs. MRO Electric and Supply maintains a comprehensive stock of new and used Control Techniques Unidrive and Control Techniques Unidrive Classic SP parts. If you need a replacement part, please call 800-691-8511 or email sales@mroelectric.com.
Code Description Action
40 Unknown error Always trips
41 Parameter does not exist Trips if #17.14=1
42 Parameter read only Trips if #17.14=1
43 Parameter write only Trips if #17.14=1
44 Parameter value over range Trips if #17.14=1and #17.17=1
45 Virtual access failed – e.g. IOLink not running Trips if #17.14=1 (access)and
#17.15=1* (all time)
46 Stack Overflow Always trips
47 Internal error Always trips
48 Internal error Always trips
49 The wrong system loaded Always trips
50 DPL Maths fault – e.g. divide by zero, overflow etc Trips if #17.14=1
51 DPL array index out of range Trips if #17.14=1
52 User-generated trip from control word Always trips *
53 DPL Program incompatible Always trips
54 DPL Overload – Clock tick too short Trips if #17.14=1
55 RS485 trip – Mode 3 Trips if #17.14=1
56 Option board and system incompatible Always trips
57 Illegal OSCall Always trips
58-59 Internal Error Trips if #17.14=1
60-69 Option generated trip Trips if #17.14=1 *
Prc2 *Watchdog Trip.See the DPL command WDOG for information
Note: The watchdog trip can be disabled by setting #17.18 to 0.
CTTG128.doc V1.0 2 04/12/05
Important Notes:
*When a trip occurs, all tasks of the DPL program will be halted (real-time tasks will
first complete) and any ERROR task is executed. The only exception to this is with trip 45, trip
52, trip 60 with certain option cards, the Watchdog trip (Prc2) and any other normal drive trips.
Other Notes
The line number is only available when the program was compiled with debugging information.
Any other trip numbers that appear are either generated by the drive itself or the DPL program.
Lastly, be sure to check out our article covering Unidrive Security Code Basics here.