The fast-paced world of industrial automation remains constantly in motion. In an environment that moves fast, the ability to diagnose and quickly control a fault remains crucial to operating an industrial machine efficiently and safely. Having a servo amplifier safety features saves money, time, and lives in the long run.
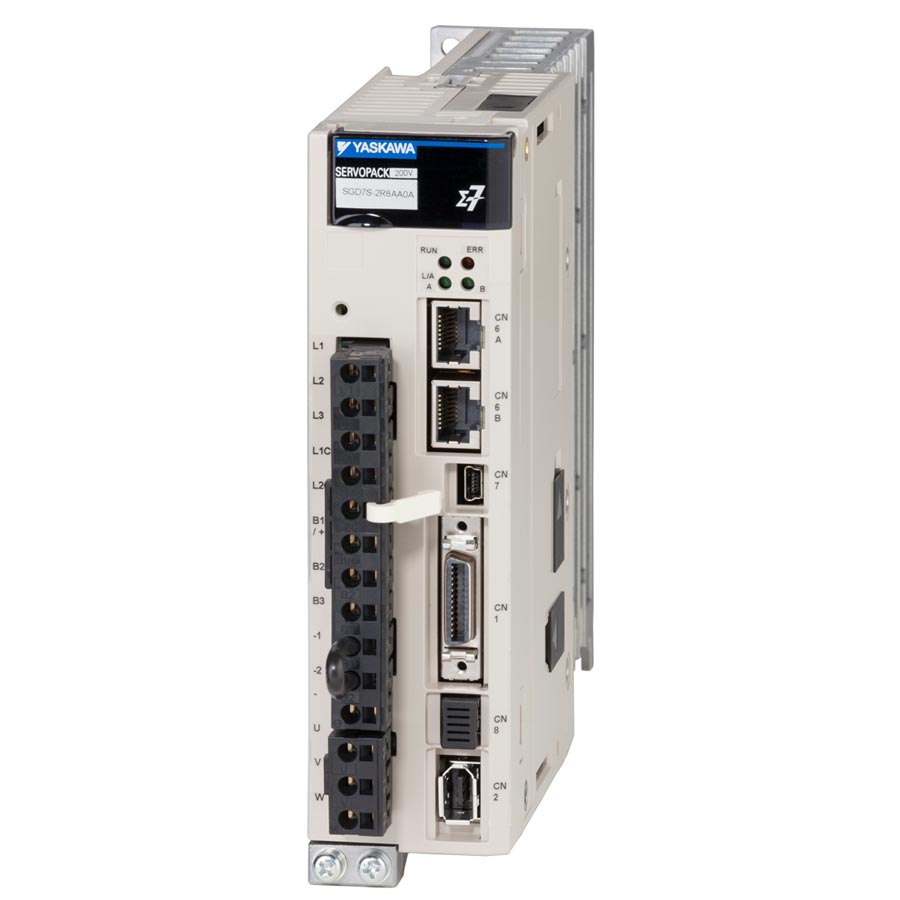
Before we get into the multiple safety features of servo amplifiers. If you are not familiar with servo amplifiers, this article covers the fundamentals of what servo amplifiers are. Definitely give it a read over!
Overcurrent Protection
Overcurrent protection exist as the most fundamental safety feature found on servo amplifiers. This mechanism prevents excessive current from flowing through the amplifier. Excessive current flows occur due to short circuits or sudden surges in demand. When an amplifier detects overcurrent,it shuts down or reduces power. This avoids overheating and potential damage to the motor and the amplifier itself. This not only preserves the lifespan of the components but also mitigates fire hazards associated with electrical overloads.
Thermal Protection
Another safety feature found in servo amplifiers, thermal protection use integrated sensors to monitor servo amplifier temperatures. These sensors initiate protective measures if temperatures rise above safety thresholds. This usually involvesreducing the power output, activating cooling fans, or even shutting down the amplifier to prevent thermal runaway and damage. Effective thermal management ensures continuous, reliable operation and extends the equipment’s service life.
Over/Under Voltage Protection
Overvoltage conditions can arise from fluctuations in the power supply or regenerative energy from the motor, potentially damaging sensitive electronic components. Undervoltage situations can impair the amplifier’s performance, leading to erratic motor behavior. By monitoring and maintaining voltage within safe limits, these protective mechanisms ensure stable and predictable operation, safeguarding both the amplifier and the connected motor.
Fault Detection and Diagonistic
Advanced servo amplifiers often incorporate fault detection and diagnostic capabilities. These systems continuously monitor operational parameters and can identify anomalies such as motor stalls, feedback errors, or communication failures. When a fault is detected, the amplifier can trigger alarms, log diagnostic information, and take corrective actions such as switching to a safe state or performing an emergency stop. This proactive approach to fault management not only prevents potential damage but also aids in troubleshooting and maintenance, reducing downtime and operational costs.
Conclusion
The safety features integrated into modern servo amplifiers are essential for protecting equipment, ensuring safe operation, and enhancing overall system reliability. Overcurrent and thermal protection, voltage regulation, and advanced fault detection are just a few examples of how these features work together to mitigate risks and extend the life of both the amplifiers and the motors they control. As technology advances, we can expect even more sophisticated safety mechanisms to emerge, further improving the safety and efficiency of servo-driven systems.
Have a Broken Servo Amplifier?
A brief guide for common Fanuc servo amplifier alarm codes can be found here
. For any inquiries regarding repair or replacement, our team is available by phone: (800) 691-8511 or by email: sales@mroelectric.com.