Circuit breakers are essential safety devices in any electrical system, protecting your home or workplace from overloading. Over time, they can wear out or malfunction, so it’s important to test them periodically to ensure they’re working correctly. In this guide, we’ll walk you through how to safely test a breaker.
Read more: How to Test a Circuit BreakerThe Importance of Testing a Circuit Breaker
There are different reasons to test circuit breakers. Where testing is most important, is in the area of safety. Regular testing of circuit breakers maintains safe electrical systems by preventing things like power surges which can damage equipment. Equipment isn’t the only safety concern that prompts regular breaker testing. Routine testing of circuit breakers can prevent fires from occurring.
Tools For Testing
When testing breakers, several tools are vital for conducting test. Among them, the tools most important are insulated gloves and a multi-meter. The insulated gloves are critical in safeguarding you from potential electrical hazards, and the multi-meter is important in circuit breaker diagnostics.
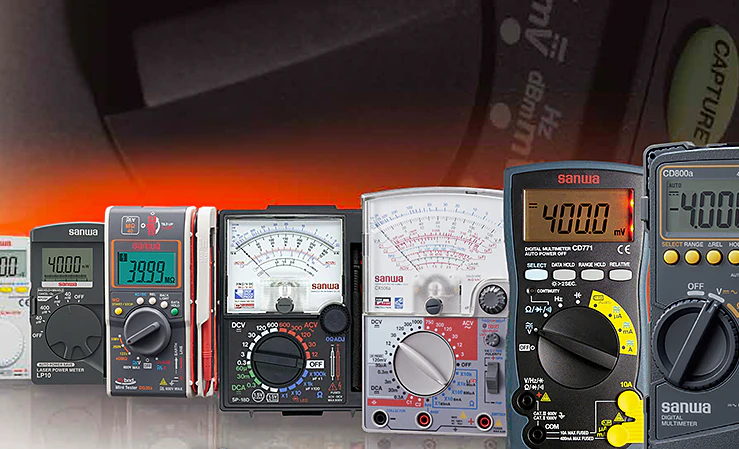
The Testing Process
Now that you know why and what equipment you’ll need to test, you’ll need to know how to test your circuit breaker. That step begins with turning off and unplugging devices along the circuit that is wired to the breaker. This prevents the security of any device or equipment you don’t want damaged. Once you’ve confirmed everything is unplugged, locate the breaker box. Usually the breaker box is located in places like a garage or basement.
The next step would be to visually scan for any signs of anything being off. That usually looks like burn marks, corrosion, or a tripped breaker. Any breaker that appear damaged should be replaced immediately. With your multimeter set to Voltage, test the breakers and circuits. A normal reading should show 120V for standard home circuits and 240V for larger circuits. A reading of 0 indicates a faulty breaker.
Perform a manual check by switching the breaker to the “ON’ position and then press the “TEST” button, the circuit should trip immediately. After tripping the breaker reset it back into the “ON” position, if it does not reset, then the breaker will need replacing.
If the breaker consistently fails voltage test, or trips without an obvious cause, call a professional electrician.
Conclusion
Testing a breaker is a simple but crucial maintenance task. By following these steps, you can ensure your electrical system remains safe and functional. If you’re unsure or encounter issues, always consult a licensed electrician for professional help.
Dirty Power
One of the biggest contributors to bad circuit breakers is what is commonly known as “dirty power”. More information about dirty power and how to prevent it can be found here.