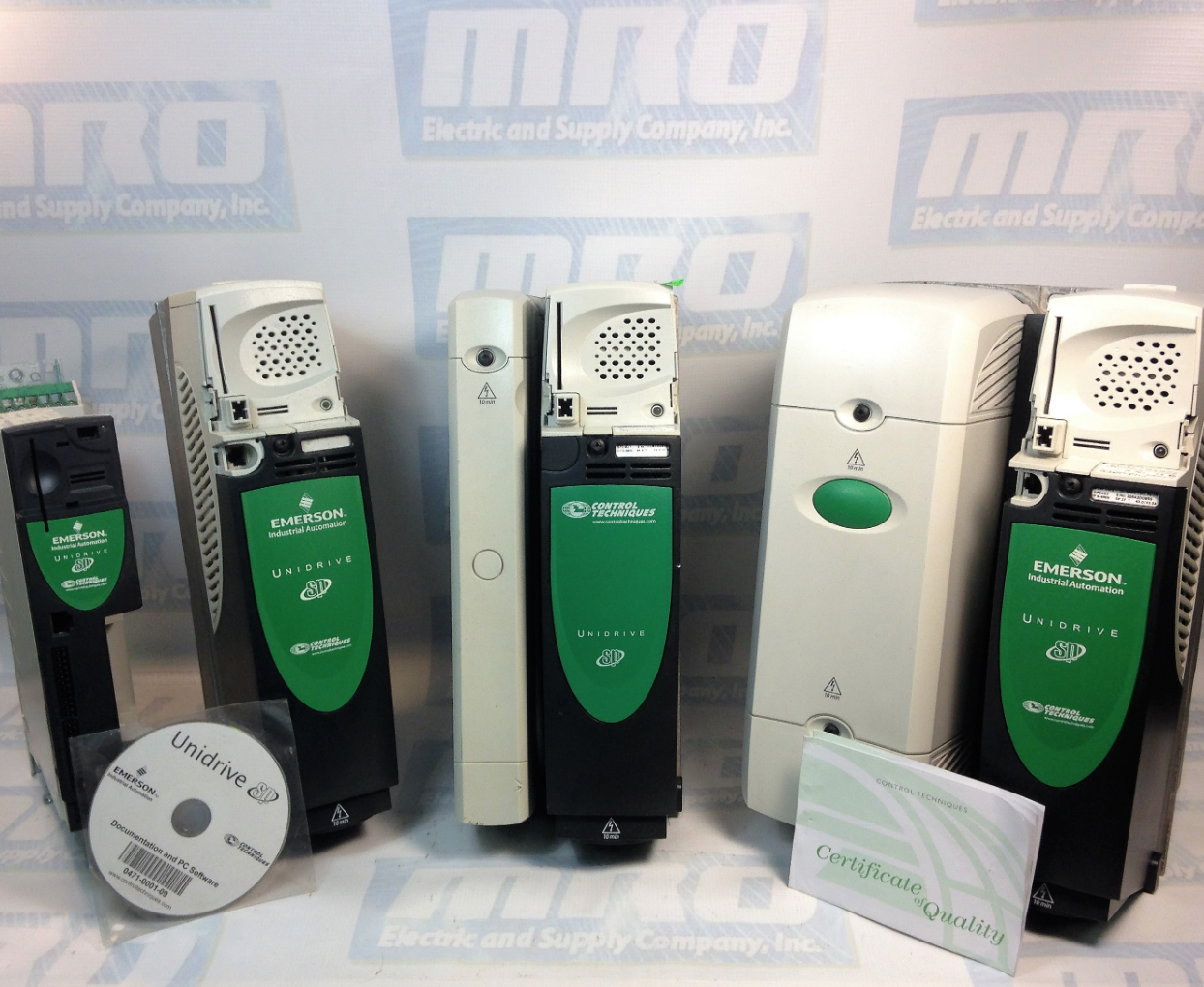
8 Standard Unidrive Macros for Uni2403 or any Classic UniDrive
Here at MRO Electric, we get a lot of questions about Unidrive Macros for the legacy Classic drives. This post explains the 8 available macros for programming a Uni2403 or another Unidrive part. You can refer to the product manual for the parameters common to all of these macros. This table shows the available Unidrive macros and their codes:
Type | Description |
Faults | What happens when a fault occurs?
- The appropriate fault reaction is initiated
- Status signal ZSW1.3 is set.
- The fault is entered in the fault buffer.
How are faults eliminated?
- Remove the original cause of the fault
- Acknowledge the fault
|
Alarms | What happens when an alarm occurs?
- Status signal ZSW1.7 is set.
- Alarms are "Self Acknowledging" meaning they are reset when the cause of the alarm has been eliminated. |
Now that you know the code for each macro, here’s a little information about how you would use each one:
Macro 1 – Easy Mode
The Easy mode macro for Unidrive classic gives the simplest operation of the drive for basic applications. It is identical to the default condition except that menu 0 has fewer parameters.
Macro 2 – Motorised potentiometer
The Motorised potentiometer macro enables the drive’s own internal motorized potentiometer to control the speed of the drive via digital inputs. A digital input selects between an analog speed reference and the motorized potentiometer reference.
Macro 3 – Preset frequencies/speeds
The Preset reference Unidrive macro enables the use of preset references to control the speed of the motor via digital inputs. A digital input selects between an analog speed reference and the present references.
Macro 4 – Torque control
The Torque control macro configures the drive for use in Torque control mode, selectable via a digital input. Analog input 1 is configured for the torque reference. When in speed control analog 2 is the speed reference. When in torque control with the drive in closed loop mode analog input 2 is the speed override reference. Enabling torque mode with the drive-in open loop mode will put the drive into pure torque control. In closed loop mode, the drive will be put into torque control with speed override.
Macro 5 – PID (set-point control)
The PID control macro enables the drive’s own internal PID controller to control the speed of the motor. Analog input 1 is configured for the main speed reference, analog input 2 is the PID reference and analog input 3 is the PID feedback. A digital input selects between an analog speed reference and the PID control.
Macro 6 – Axis-limit control
The Axis limit control macro configures the drive for use with limit switches so that the drive is stopped when a position limit has been reached. The speed reference can be either unipolar or bipolar.
Macro 7 – Brake control
The brake control macro configures the drive to apply or release a mechanical brake on a motor in a crane or hoist application. The drive issues a brake release signal via a digital output when the relevant conditions are met.
Macro 8 – Digital lock/shaft orientation
^Only available in closed loop vector or servo operating modes.
Digital lock:
The drive operates as a slave in a closed loop master-slave system. The slave motor is digitally locked to the master motor.
Shaft orientation:
The motor speed is controlled in the same way as for default operation, but the motor shaft can be orientated to a specified angular position before and/or after running the motor.
MRO Electric and Supply has new and refurbished Control Techniques parts available including Control Techniques Unidrive and Unidrive SP series. We also offer repair pricing. For more information, please call 800-691-8511 or email sales@mroelectric.com.