The Schneider Electric / Modion HMI-STU-855 is a 5.7 inch touch panel screen with a Magelis operating system and CPU ARM9 processor. It uses a QVGA TFT color touchscreen with a pixel resolution of 320 x 240 pixels. It uses an external supply source of 24 volts and consumes 6.8 watts of power. It has 16 MB of application battery with 64 kB available to back up data. The HMISTU855 is able to download a number of protocols including Modbus, Modbus TCP/IP, Uni-TE, and 3rd party protocols. When using the HMISTU855, all connections to the communication ports on the bottom and sides of the unit must not put large amounts of stress on the ports. Be sure to securely attach communication cables to the panel or cabinet. Use only RJ45 cables with a functioning locking tab.
Critical detected alarm indicators and systematic function require independent and redundant protection hardware or mechanical interlocks. It is important that when power is cycled, the user waits at least 10 seconds before restoring power. Switching the power on and off quickly can damage the unit. The interface is connected to remote equipment using a RS232C or RS-485 cable. The connector that is used is a RJ45-8 pin type. The using a long PLC cable to connect the unit, a difference of electric potential can be observed between the cable and the ground, even when connected to a ground. The serial port on the HMI-STU-855 is not isolated. The signal ground and frame ground terminals are connected inside the unit. When setting up the RS-485 communication, the cable diagram for some equipment may need polarization on the terminal side. This terminal does not need any special setting because it can handle polarization automatically.
MRO Electric and Supply Company stocks many Modicon Magelis HMIs and panels, including the HMI-STU-855. For for information or to request a quote, please email sales@mroelectric.com or call 800-691-8511.
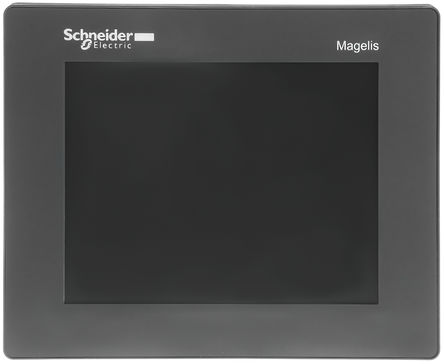