Human Machine Interfaces (HMIs) play a crucial role in modern industrial automation, allowing operators to monitor and control various processes. Schneider Electric’s Magelis HMIs are renowned for their reliability and performance. However, like any technology, they can encounter issues that require troubleshooting. In this comprehensive guide, we will explore common problems with Schneider Electric Magelis HMIs and provide step-by-step solutions to help you keep your operations running smoothly.
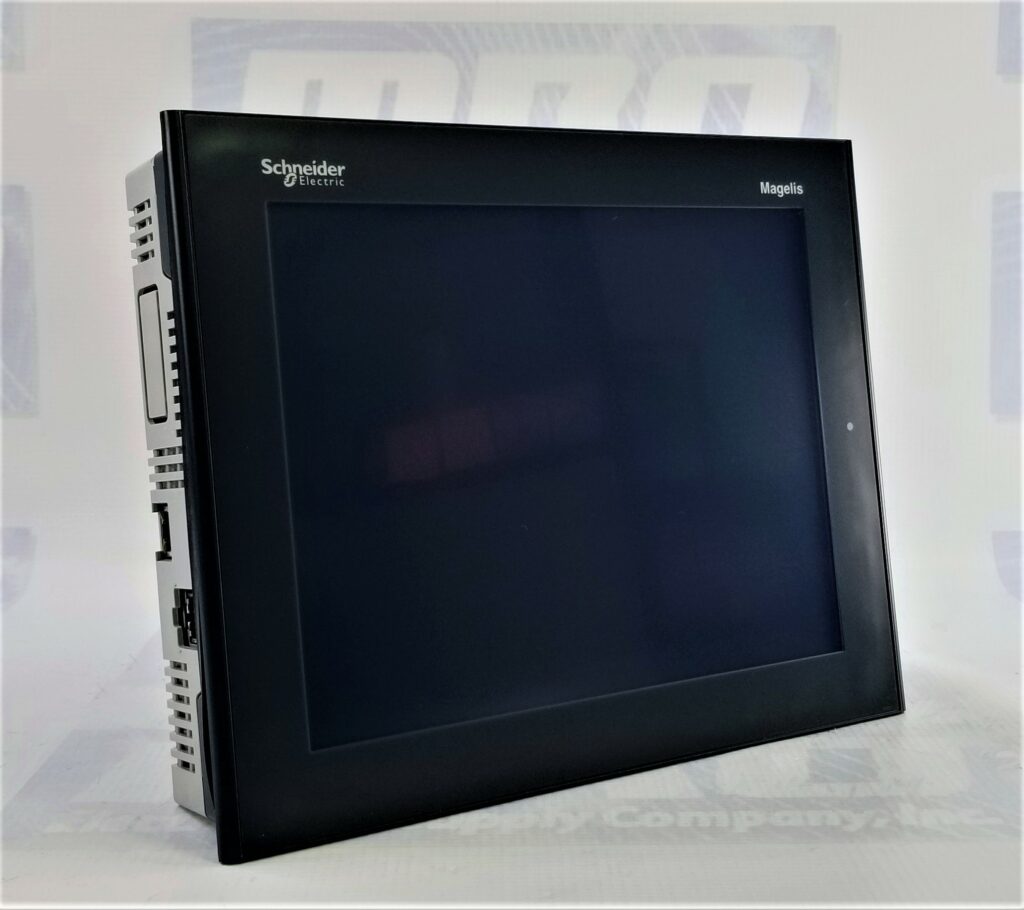
Understanding Schneider Electric Magelis HMIs
Before diving into troubleshooting, it’s essential to have a basic understanding of Schneider Electric Magelis HMIs. These devices are used in a wide range of industries, including manufacturing, energy, and infrastructure. They provide an intuitive interface for operators to interact with machines, view real-time data, and make informed decisions.
Magelis HMIs come in various models and sizes, from compact panels to advanced touchscreens. They are known for their robustness, high-quality displays, and compatibility with Schneider Electric’s automation solutions. However, even the best HMIs can face issues, and knowing how to troubleshoot them can save time and resources.
Common Schneider Electric Magelis HMI Issues
1. HMI Display Problems
Symptom:
- Blank or distorted screen.
- Touchscreen not responding.
- Flickering or frozen display.
Solution:
- Check Power Supply: Ensure the HMI is receiving adequate power. Verify connections to the power source and power supply unit.
- Screen Calibration: If the touchscreen is unresponsive or inaccurate, recalibrate it following the manufacturer’s instructions.
- Graphics Driver: Update the graphics driver to the latest version compatible with your HMI model.
- Hardware Issues: Inspect the HMI for physical damage or loose connections. Replace damaged components if necessary.
2. Communication Problems
Symptom:
- HMI unable to communicate with PLC or other devices.
- Error messages related to communication.
Solution:
- Check Cables and Connections: Verify that all cables and connections between the HMI and other devices (PLC, sensors, etc.) are secure and undamaged.
- Communication Settings: Ensure that the communication settings (baud rate, protocol, IP addresses) on the HMI match those of the connected devices.
- Firewall and Security: Disable or adjust firewall settings on networked devices to allow communication.
- Network Troubleshooting: If using a networked HMI, diagnose network issues such as IP conflicts or network congestion.
3. Software and Programming Errors
Symptom:
- Unexpected program crashes or errors.
- Incorrect data displayed on the HMI.
Solution:
- Software Updates: Make sure you are using the latest version of the HMI software. Update if necessary.
- Check Logic and Scripting: Review and debug the logic and scripts used in your HMI application. Ensure they are error-free.
- Backup and Restore: Regularly backup your HMI project. If issues arise, you can restore from a known-good backup.
- Memory Management: Check available memory on the HMI. Clear unnecessary files and logs that might be consuming resources.
4. Hardware Failures
Symptom:
- HMI hardware components (buttons, LEDs, etc.) not functioning correctly.
- Unusual noises or smells from the HMI.
Solution:
- Component Replacement: If specific hardware components are malfunctioning, replace them with compatible parts.
- Overheating: Check for overheating issues by ensuring proper ventilation. Clean any dust or debris that might be blocking airflow.
- Inspect Internal Components: If comfortable with electronics, open the HMI enclosure (if applicable) and inspect internal components for damage or loose connections.
5. Security Concerns
Symptom:
- Unauthorized access to the HMI.
- Concerns about cybersecurity threats.
Solution:
- Password Protection: Ensure that your HMI is password-protected. Change default passwords and enforce strong password policies.
- Firewall and Security Measures: Implement firewalls, access control lists, and other security measures to protect your HMI from external threats.
- Regular Updates: Keep the HMI software and firmware up to date to patch security vulnerabilities.
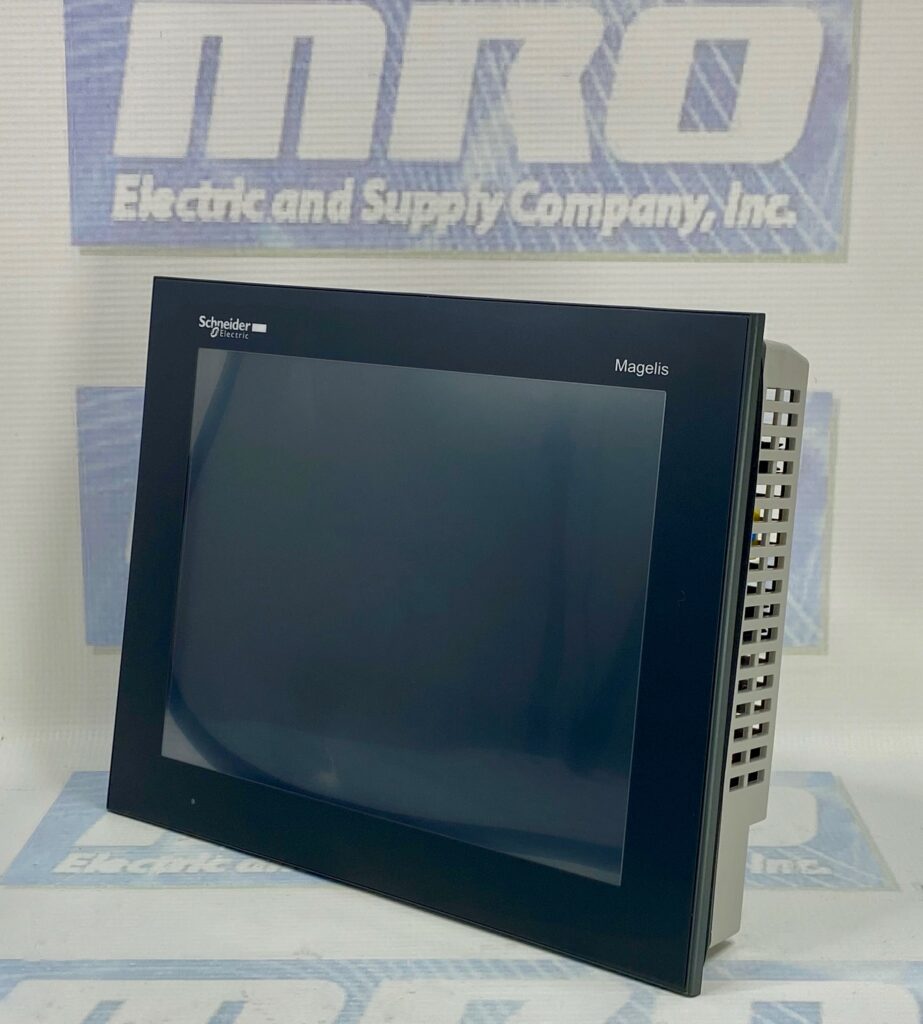
Advanced Troubleshooting Techniques
For more complex issues that cannot be resolved using the above solutions, consider these advanced troubleshooting techniques:
- Log Analysis: Examine system logs and error messages to identify the root cause of the problem.
- Factory Reset: As a last resort, perform a factory reset of the HMI, but only after backing up essential data.
- Technical Support: Contact Schneider Electric’s technical support or consult their knowledge base for assistance with specific issues.
- Hardware Diagnostics: Use diagnostic tools and equipment to test the HMI’s hardware components thoroughly.
Preventive Maintenance
Preventing issues is as important as troubleshooting them. Here are some preventive maintenance tips for Schneider Electric Magelis HMIs:
- Regularly clean the touchscreen and enclosure to prevent dust and dirt buildup.
- Monitor system logs and performance regularly to catch issues before they become critical.
- Update software and firmware as recommended by Schneider Electric.
- Train operators and maintenance personnel on proper HMI usage and basic troubleshooting.
Conclusion
Schneider Electric Magelis HMIs are vital components in industrial automation and keeping them in optimal condition is crucial for efficient operations. With the troubleshooting techniques and preventive maintenance tips outlined in this guide, you’ll be better equipped to address common HMI issues and ensure the continued success of your automation processes. Remember, when in doubt, consult Schneider Electric’s technical support for expert assistance.
Updated on January 31, 2024 by Joe Kaminski