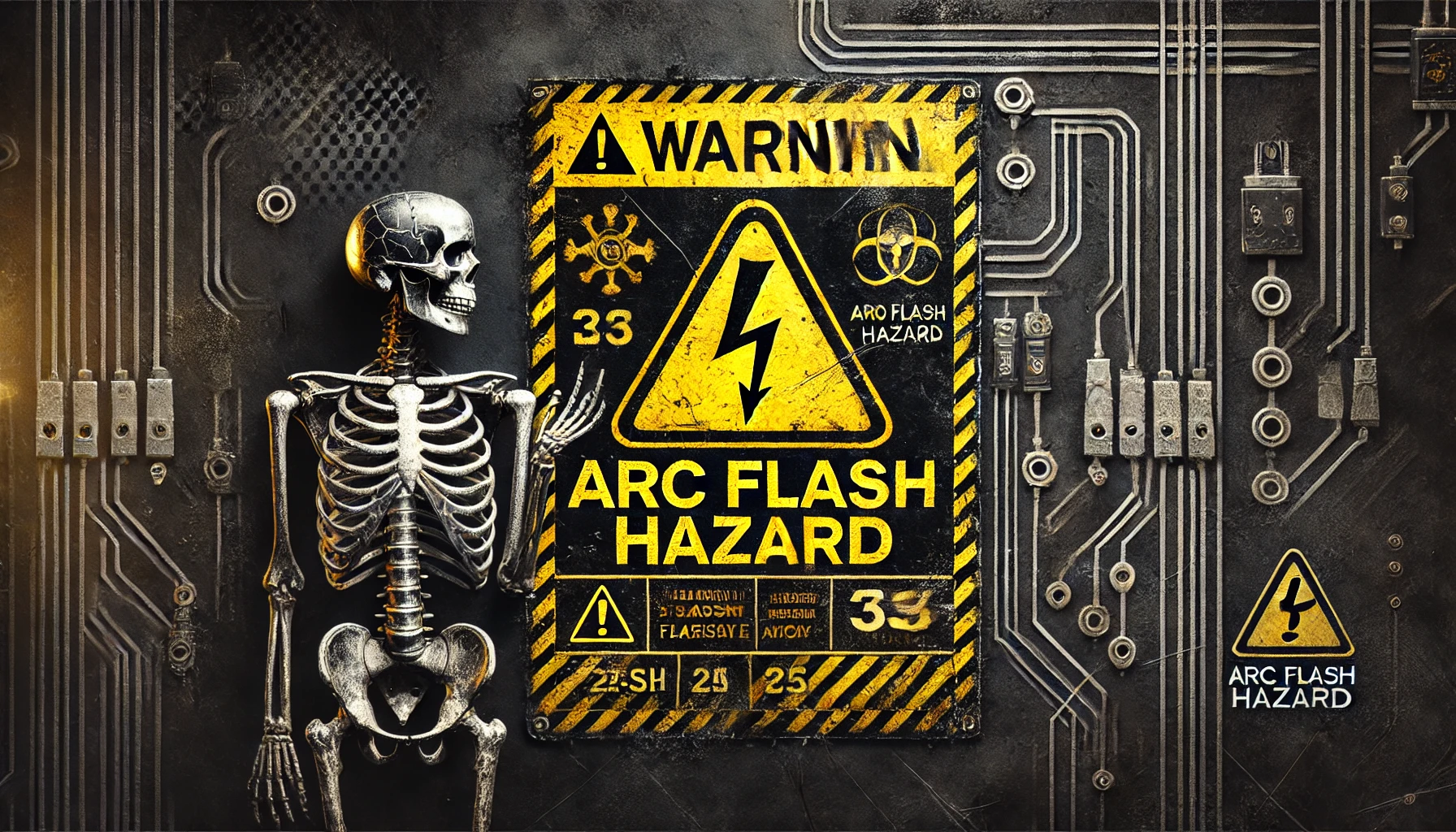
Arc flash incidents are among the most dangerous hazards in the electrical industry, posing serious risks to personnel and equipment. Properly labeled equipment can help prevent injuries and fatalities associated with arc flash incidents. For this reason, the National Fire Protection Association (NFPA) and the National Electrical Code (NEC) have established rigorous guidelines for arc flash labeling. This article explores the legal and safety requirements for arc flash labels, with a focus on NFPA 70E and NEC standards, while discussing the critical role these labels play in workplace safety and regulatory compliance.
Read more: Legal and Safety Requirements Regarding Arc FlashesWhat is an Arc Flash?
As we discussed in a previous post, an arc flash occurs when an electric current leaves its intended path, traveling through the air from one conductor to another, or to the ground. This incident can result in temperatures of up to 35,000°F, releasing intense heat, light, sound, and pressure that can cause severe burns, hearing loss, and even death. Recognizing and controlling arc flash hazards is essential for worker safety, and labels play a crucial role in alerting workers to the potential dangers of working with energized equipment.
Legal and Regulatory Requirements for Labels
NFPA 70E: Standard for Electrical Safety in the Workplace
The NFPA 70E is a key standard that provides guidelines for electrical safety in the workplace. It outlines safety practices and requirements for identifying arc flash hazards. It determines appropriate personal protective equipment (PPE), and providing training for workers who may be exposed to electrical hazards.
Under NFPA 70E, labels must include specific information to inform workers about the potential hazards associated with electrical equipment. These requirements include:
- Nominal System Voltage: Identifies the voltage level of the equipment, allowing workers to determine the level of PPE and other safety precautions needed.
- Arc Flash Boundary: Defines the minimum safe working distance from the equipment that requires protection.
- Incident Energy Level or PPE Category: Indicates the level of energy (calculated in calories per square centimeter) potentially released in an arc flash, along with the corresponding PPE level required to protect workers.
It is imperative to place these labels on electrical panels, switchboards, motor control centers, and other equipment where arc flash risks exist. Compliance with NFPA 70E standards not only enhances worker safety but also reduces liability and helps companies avoid potential regulatory penalties.
NEC: National Electrical Code
The National Electrical Code (NEC), also known as NFPA 70, provides guidelines for electrical installations to promote safe electrical practices. Article 110.16 of the NEC addresses labeling requirements, stipulating that electrical equipment likely to require examination, adjustment, servicing, or maintenance while energized must be marked to warn qualified personnel of potential hazards.
The NEC requires that arc flash labels contain a warning message indicating the presence of an arc flash hazard. However, it does not mandate specific details like incident energy levels or PPE requirements. The intent of NEC labeling requirements is to ensure that anyone working on or near the equipment is aware of potential hazards, while NFPA 70E provides the detailed information necessary for personnel safety.
Why Proper Arc Flash Labeling Is Essential
Proper arc flash labeling is crucial for multiple reasons, including the protection of workers, ensuring compliance with regulations, and reducing liability for organizations. Here are the primary reasons why proper arc flash labeling is essential:
- Enhances Worker Safety: Accurate and comprehensive arc flash labels help workers identify hazards and determine the appropriate safety measures, PPE, and distance requirements. In the event of an arc flash, properly labeled equipment can prevent or significantly reduce injuries by guiding workers on how to protect themselves.
- Facilitates Compliance with Regulatory Standards: Compliance with NFPA 70E and NEC is mandatory for organizations. Failing to adhere to these standards can result in legal consequences, regulatory fines, and increased scrutiny from safety inspectors. By meeting labeling requirements, companies can demonstrate a commitment to workplace safety and regulatory compliance.
- Improves Risk Management and Liability Protection: In the event of an arc flash incident, proper labeling can serve as evidence that an organization took reasonable steps to protect its employees. Failure to label equipment correctly increases liability in the event of an incident. Proper labeling helps mitigate this risk and shows due diligence in maintaining a safe workplace.
- Supports Effective Training and Awareness: Arc flash labels also play an educational role, providing visual reinforcement of electrical safety practices. When combined with formal training, these labels reinforce key safety information, helping workers remember and follow established protocols.
- Promotes Maintenance Best Practices: Arc flash labels indicate when equipment needs de-energizing or when a specific operation requires specific protective measures. This information not only protects workers but also supports maintenance planning. It also ensures that operators follow proper procedures to reduce equipment downtime and improve operational efficiency.

Arc Flash Labeling Best Practices
When implementing arc flash labels, consider the following best practices to ensure compliance and maximize effectiveness:
- Regularly Update Labels: Labels should be reviewed and updated whenever there is a change in the electrical system, such as equipment upgrades or modifications that could alter the hazard level.
- Use Durable Materials: Labels should be made from materials that can withstand harsh conditions, including high temperatures, moisture, and chemical exposure, to ensure they remain legible and effective over time.
- Maintain Consistency in Label Design: Consistent labeling formats and terminology across equipment help workers quickly identify and understand hazards. Clear symbols and standardized language make labels more accessible and effective.
- Incorporate Labels into Training Programs: Safety training should include information on reading and understanding arc flash labels, as well as practical demonstrations to reinforce key safety practices.
Conclusion
Proper arc flash labeling, as mandated by NFPA 70E and NEC, is vital for workplace safety and regulatory compliance. These labels are not merely informational—they are crucial safety tools that guide workers on protective measures and ensure that hazards are clearly communicated. By following established standards and best practices, companies can protect their workers, fulfill their legal obligations, and create a safer work environment.
Updated on November 19, 2024 by Ken Cheng