Since the mid-twentieth century Computer Numerical Control (CNC) machines have revolutionized the manufacturing industry. They have done so by automating and enhancing precision in the production of various components. Industries that often use them include aerospace, automotive, and electronics to create intricate and accurate parts.
Read more: Components and Functions of a CNC MachineFunction
A CNC machine is basically a sophisticated tool that translates digital instructions into precise physical movements. It allows the user to interface with
The primary functions of a CNC machine include:
- Digital Control: Computer programs that dictate the tool’s movements and actions. These programs contain detailed instructions for the machining process.
- Automated Precision: One of the key advantages of CNC machines is their ability to execute repetitive tasks with unparalleled precision. The automation eliminates the margin of error associated with manual operations, resulting in consistently high-quality products.
- Versatility: CNC machines can perform a wide range of tasks, from cutting and milling to drilling and engraving. Their versatility makes them indispensable in various manufacturing processes.
History
The roots of CNC technology can be found in the development of numerical control systems during the mid-twentieth century. Around this time, the aviation industry emerged as a significant catalyst for CNC innovation. Engineers sought a more efficient and precise way to machine complex components for aircraft. This led to the birth of numerical control as a solution to automate machine tools.

The 1940’s kicked off the history of the CNC machine with the introduction of punched tape systems. These systems allowed engineers to input numerical instructions into machine tools, automating certain aspects of the machining process. It wasn’t until the 1950s that the concept of CNC truly began to take shape. John T. Parsons, often regarded as the father of CNC, played a pivotal role in advancing the technology. Parsons, along with Frank L. Stulen, developed the concept of controlling machine tools through punched cards, laying the groundwork for the CNC machines we know today.
During the 1960s, the Massachusetts Institute of Technology (MIT) introduced the concept of direct numerical control (DNC). As the technology matured, industries beyond aviation started adopting CNC machines. The 1970s saw the integration of computers into CNC systems, allowing for more sophisticated programming and control. This integration, allowed the machines to become increasingly versatile and accessible. This led to widespread CNC adoption across various manufacturing sectors.

CNC machines evolved beyond milling to encompass a wide range of machining operations. This includes turning, grinding, and electrical discharge machining (EDM). Presently, CNC machines are at the forefront of advanced manufacturing, shaping industries ranging from automotive and aerospace to electronics and healthcare.
Parts
While there are varying models and designs, CNC machines generally are made of several different parts. These parts are crucial to the function of the CNC.
- Control Unit:
- Computer: The brain of the CNC machine, the computer processes the instructions from the program and translates them into electrical signals.
- Control Panel: Operators use the control panel to input data, set parameters, and monitor the machine’s performance.
- Drive System:
- Motors: Drives the movement of the cutting tool along the specified path. Common types include stepper motors and servo motors.
- Ball Screws/Rack and Pinion: These components convert the rotational motion of the motors into linear motion, guiding the tool precisely along the desired path.
- Tooling System:
- Cutting Tool: The cutting tool is an essential component that physically shapes the material. Different tools are used for various machining operations.
- Tool Changer: In machining processes that require multiple tools, a tool changer automates the process of switching between tools.
- Work Holding Device:
- Vise or Chuck: The workholding device secures the raw material in place during machining. It ensures stability and accuracy throughout the cutting process.
- Coolant System:
- Coolant Tank and Pump: Machining generates heat, and a coolant system helps dissipate this heat, preventing damage to the tool and workpiece. It also aids in chip removal.
- Axis System:
- Linear Guides: These guides facilitate the smooth movement of the machine’s axes. They play a crucial role in maintaining accuracy during machining.
- Axis Motors: CNC machines typically operate in three or more axes (X, Y, Z), and each axis has its motor for precise control.
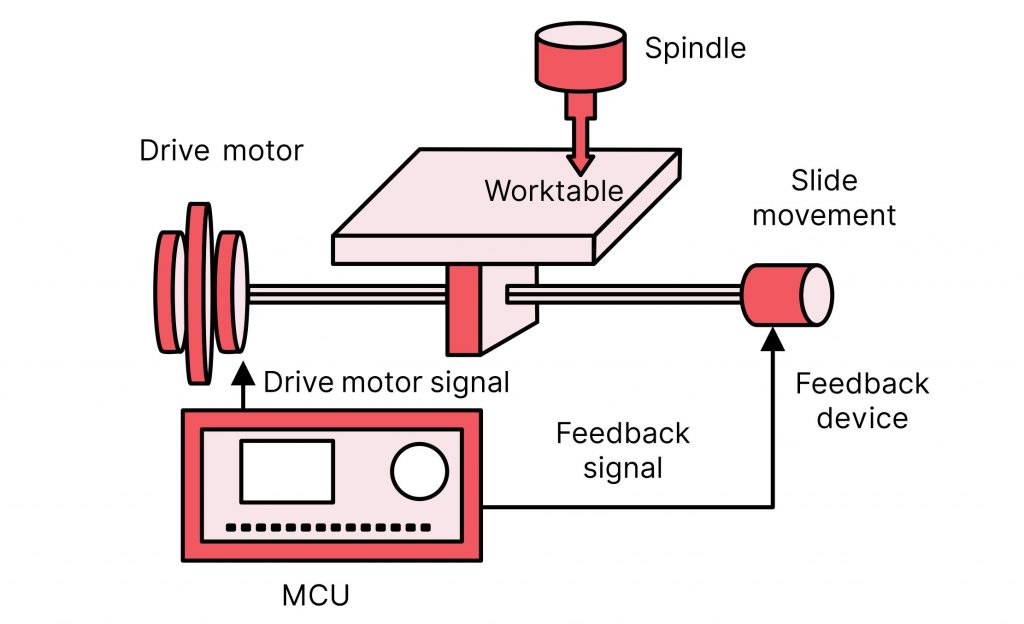
Conclusion
Understanding the functions and components of a CNC machine is essential for those involved in the design and operation of these advanced manufacturing tools. As technology continues to advance, CNC machines are likely to play an even more pivotal role in shaping the future of manufacturing processes.
Updated on March 7, 2024 by Ken Cheng